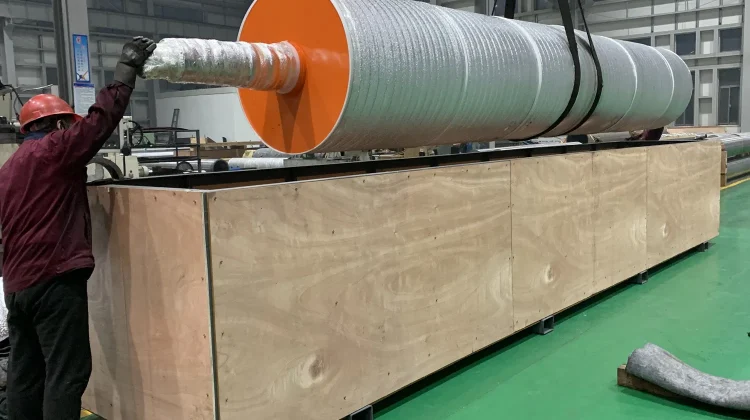
Maximizing Performance with Paper Machine Rolls
In the complex world of papermaking, where precision and efficiency are paramount, certain components stand out as truly foundational. Among these, paper machine rolls are arguably the unsung heroes, forming the very backbone of the entire process from the initial dewatering stages right through to the final finishing. Have you ever stopped to consider just how many rolls are involved in transforming a watery pulp mixture into the smooth, finished paper we use every day? It’s an astonishing number, often hundreds, each meticulously engineered to perform a specific, vital task. Their condition directly impacts paper quality, production speed, energy consumption, and ultimately, profitability. Frankly speaking, without properly functioning rolls, a paper machine is little more than a collection of pipes and steel. Understanding their function, challenges, and maintenance is absolutely critical for anyone involved in this industry, whether you’re operating the machine, maintaining it, or managing the mill.
The Diversity and Function of Paper Machine Rolls
The journey of paper pulp through a modern machine is a carefully orchestrated sequence of steps, each relying heavily on different types of paper machine rolls. From the initial formation section, where water is drained, through the press section, where more moisture is mechanically squeezed out, into the dryer section using heated cylinders, and finally through the calender for surface finishing and the reel for winding – each stage utilizes specialized rolls. Press rolls, for instance, apply immense pressure, sometimes hundreds of pounds per linear inch, to dewater the sheet and consolidate the fibers. Their surface properties, whether grooved, blind-drilled, or covered with advanced materials, are crucial for effective water removal and preventing sheet crushing. Dryer cylinders, often large, cast iron rolls heated internally by steam, are responsible for evaporating the remaining moisture. Their surface needs to be smooth and clean for efficient heat transfer. Then there are calender rolls, which improve the paper’s smoothness, gloss, and thickness uniformity. Each type of roll, from the massive, heavy press rolls to the smaller guide and felt rolls, plays an indispensable part in ensuring the continuous, high-speed production of a consistent, quality product. It’s this incredible diversity of roles and designs that makes the management of paper machine rolls a complex, yet fascinating, challenge.
Understanding Different Roll Types and Their Specific Demands
Delving deeper, the specific demands placed on each roll type highlight why specialized knowledge is key. Press rolls face high mechanical loads and chemical exposure from process water, requiring robust construction and often resilient, chemical-resistant roll covers. Their geometry, including crowning (a slight taper or bulge) and balancing, is vital to ensure uniform nip pressure across the width of the paper web, preventing uneven dewatering and caliper variations. Dryer cylinders, while not under extreme mechanical load from the sheet itself, must withstand high internal temperatures and pressures, as well as the constant abrasive contact of the paper web and dryer fabrics. Their structural integrity and thermal conductivity are paramount. Calender rolls, which often operate at high temperatures and pressures to compact and smooth the sheet, require extremely hard, smooth surfaces, often chilled iron or composite materials. Even seemingly simple guide rolls or felt rolls, which support and guide the paper web and fabrics, must be precisely balanced and run true to prevent web breaks and fluttering. Understanding these distinct operating environments and stresses is the first step in effective maintenance and selection of the right paper machine rolls for each position.
The Silent Saboteurs: Wear, Damage, and Roll Surface Issues
Even with the best design and materials, the demanding environment of a paper machine inevitably leads to wear and potential damage to the rolls. Constant friction from the paper web, felts, and fabrics, combined with high pressures, temperatures, and often corrosive process chemicals, takes its toll. Roll covers can wear unevenly, leading to profile variations that cause uneven dewatering in the press section or inconsistent finishing in the calender. Impact damage from foreign objects entering the machine can cause dents or gouges, which create defects in the paper web and can propagate further damage. Corrosion, particularly in wet end and press section rolls, can weaken the roll shell or damage the surface. Even seemingly minor issues like accumulation of sticky deposits can negatively affect paper quality and machine runnability. These issues aren’t always immediately obvious during operation, but they silently degrade performance, reduce paper quality, and increase the risk of costly downtime. Catching these problems early through diligent inspection and monitoring is far more cost-effective than dealing with their consequences.
Identifying Common Roll Defects and Their Impact on Paper Quality
Identifying common defects on paper machine rolls is a critical skill for maintenance and production personnel. Uneven wear patterns, for example, can manifest as streaks, caliper variations, or uneven moisture profiles in the paper. Cracks or chips in roll covers can create repetitive marks or weak points in the sheet, potentially leading to breaks. Corroded surfaces can cause the paper to stick, disrupting the web path and potentially pulling fibers, affecting strength and appearance. Bearings that are worn or improperly lubricated can lead to vibration, causing barring or chatter marks on the paper surface, or even catastrophic failure of the roll itself. Understanding the visual signs on the roll and correlating them with specific paper defects is key to troubleshooting. Is that caliper variation across the sheet linked to the wear profile on the press roll? Is that repetitive mark caused by a chip on a calender roll? Answering these questions quickly is vital for maintaining high paper quality and minimizing waste. This requires a keen eye and often specialized tools for inspection.
Proactive Strategies for Maintenance of Paper Machine Rolls
Given the critical nature of rolls and the potential for damage, proactive maintenance is not just recommended, it’s essential for successful paper mill operations. Simply running rolls until failure is a recipe for unexpected downtime and significant financial loss. A comprehensive maintenance of paper machine rolls program should include regular inspections, both while the machine is running (observing vibration, noise, temperature) and during planned shutdowns (visual inspection, dimensional checks, non-destructive testing). Techniques like ultrasonic testing, eddy current testing, and thermography can reveal hidden issues like subsurface cracks, corrosion under covers, or bearing overheating before they become critical. Roll grinding, performed at regular intervals or when wear exceeds acceptable limits, is crucial for restoring the correct profile and surface finish. Proper roll balancing is also vital, especially for high-speed machines, to minimize vibration and extend bearing life. Lubrication of roll bearings with the correct type and amount of grease or oil is fundamental. Implementing a scheduled maintenance program based on machine speed, operating hours, roll type, and coating material can significantly extend the lifespan of rolls and improve machine reliability. It’s about shifting from a reactive fix-it-when-it’s-broken approach to a predictive and preventive strategy.
Implementing Effective Inspection and Grinding Practices
Effective inspection is the cornerstone of proactive roll maintenance. This goes beyond just looking at the roll surface. It involves precise measurements of diameter, length, and profile using specialized tools. Profile measurements are crucial for assessing wear and verifying crowning. Non-destructive testing methods allow technicians to look beneath the surface, checking for internal flaws in metal rolls or delamination in composite covers. Recording these measurements and observations over time creates a valuable history for each roll, helping to predict when grinding or other interventions will be needed. When grinding is required, it must be performed with high precision by skilled technicians using specialized grinding equipment. The goal is not just to restore a smooth surface, but to achieve the exact specified profile and dimension. An improperly ground roll can cause more problems than it solves, leading to uneven nips, poor dewatering, or inconsistent finishing. The frequency of grinding depends on the roll’s position, operating conditions, and the type of cover, if any. Developing clear standards and procedures for both inspection and grinding is vital for maintaining peak roll performance and paper quality.
Optimizing Paper Machine Performance Through Roll Management
Beyond simply maintaining rolls, the concept of optimizing paper machine performance places rolls within the broader context of machine operation and efficiency. This involves more than just keeping rolls in good condition; it’s about selecting the right rolls for the job, ensuring they are properly installed and aligned, and understanding how their performance impacts the entire production chain. For instance, optimizing nip pressures in the press section based on roll type and paper grade can dramatically improve dewatering, reducing the energy needed in the dryer section. Choosing advanced roll covers with specific surface properties can enhance sheet release, improve fiber support, and resist wear or chemical attack. Utilizing online monitoring systems that track roll vibration, bearing temperatures, and even roll profile in some cases allows operators to detect anomalies early and schedule interventions before they lead to catastrophic failure. Proper roll crowning, which compensates for the deflection of the roll under load, is also critical for achieving uniform cross-machine profiles. Effective roll management is an integrated approach that considers roll design, material science, maintenance practices, and operational parameters to maximize machine output and paper quality.
Leveraging Technology and Data for Smarter Roll Management
In today’s data-driven world, technology offers powerful tools for smarter roll management. Implementing computerized maintenance management systems (CMMS) allows mills to schedule and track roll inspections, maintenance history, grinding cycles, and performance data for each individual roll. This data can be analyzed to identify trends, predict maintenance needs more accurately, and optimize inventory of spare rolls. Online monitoring systems using sensors for vibration, temperature, and acoustics provide real-time data on roll health, enabling condition-based maintenance rather than relying solely on fixed schedules. Advanced algorithms can analyze this data to detect subtle changes indicative of impending failure, giving maintenance teams valuable lead time to plan interventions. Furthermore, sophisticated simulation software can help predict roll behavior under various operating conditions, aiding in the selection of appropriate roll covers and crowning profiles. Embracing these technologies transforms roll maintenance from a routine task into a strategic activity aimed at maximizing uptime and product quality. It’s an investment that pays significant dividends in operational efficiency and reduced costs.
Choosing the Right Types of Paper Machine Rolls and Supplier
Selecting the appropriate types of paper machine rolls for each position and paper grade is a critical decision that impacts machine performance for years. It’s not a one-size-fits-all scenario. Factors such as operating speed, nip pressure, temperature, moisture levels, chemical environment, and the specific paper grade being produced all influence the ideal roll material, construction, and surface treatment. For example, a high-speed machine producing lightweight coated paper will require different press roll covers and calender rolls than a machine producing heavy linerboard. The choice between cast iron, steel, granite, or composite roll shells, and the selection of rubber, polyurethane, ceramic, or composite roll covers, depends entirely on the specific application and desired performance characteristics. Partnering with a knowledgeable supplier is paramount here. A good supplier doesn’t just sell rolls; they offer expertise in roll design, application engineering, and material science. They can help evaluate your specific needs, recommend the best roll solutions, and provide insights into optimizing performance based on their experience across different mills and machine types. This partnership ensures that the significant investment in rolls yields the best possible return in terms of machine efficiency and paper quality.
Addressing Challenges and Ensuring Long-Term Roll Performance
Ensuring the long-term performance of paper machine rolls is an ongoing process that requires vigilance and expertise. Challenges like preventing vibration, managing roll cover wear, mitigating corrosion, and addressing bearing issues are constants in the papermaking world. Vibration, for instance, can be caused by imbalance, misalignment, bearing issues, or even aerodynamic forces at high speeds. Identifying and correcting the source of vibration is crucial to prevent damage to the rolls and other machine components, as well as to maintain paper quality. Roll cover management is another key area; selecting covers that resist wear and buildup, applying them correctly, and regrinding them at the optimal time are all vital steps. Preventing corrosion, particularly on metal rolls, requires understanding the process water chemistry and potentially using protective coatings or materials. Bearing maintenance, including proper lubrication, alignment, and timely replacement, is fundamental to roll longevity and preventing costly failures. To be honest, mastering these areas requires a deep understanding of both mechanical engineering principles and the specifics of the papermaking process. It’s an area where specialized knowledge and experience make a significant difference in operational reliability and cost efficiency.
Partnering for Success: How Our Expertise Helps
Understanding these challenges is one thing; having a reliable partner to help navigate them is another. This is where specialized knowledge and comprehensive services become invaluable. We understand that paper machine rolls are complex assets requiring specialized attention. Our expertise lies in providing not just high-quality rolls designed for specific applications, but also the supporting services that ensure their optimal performance throughout their lifecycle. This includes expert consultation on roll selection, precision roll grinding and balancing services, application of advanced roll covers, and comprehensive roll inspection and diagnostic capabilities. We help mills identify potential issues early, develop tailored maintenance plans, and implement solutions that reduce downtime, improve paper quality, and lower operational costs. Our approach is collaborative, working with mill personnel to understand their unique challenges and provide solutions that deliver tangible results. By leveraging our knowledge in roll technology and maintenance best practices, paper mills can achieve greater efficiency and profitability from their operations. We are dedicated to helping you maximize the return on your investment in these critical machine components.
Conclusion: Investing in the Health of Your Paper Machine Rolls
In conclusion, the performance of paper machine rolls is intrinsically linked to the overall success of a paper mill. From dewatering and drying to finishing and winding, these critical components are constantly under stress, and their condition dictates everything from machine speed and efficiency to the quality of the final paper product. Proactive maintenance, informed by regular inspection, precise grinding, and strategic use of technology, is not an optional expense but a necessary investment in operational reliability and profitability. Understanding the different types of rolls, their specific functions, and the common issues they face allows mills to implement effective strategies for wear management, vibration control, and damage prevention. Selecting the right rolls for specific applications and partnering with knowledgeable experts for maintenance and support further enhances performance and extends asset life. What steps are you taking today to ensure the optimal health and performance of your paper machine rolls? Ensuring these critical assets are in peak condition is a clear path to achieving higher productivity, better paper quality, and reduced operating costs. Don’t wait for a costly failure to realize the importance of comprehensive roll management.
For more detailed information, please visit our official website: paper machine rolls