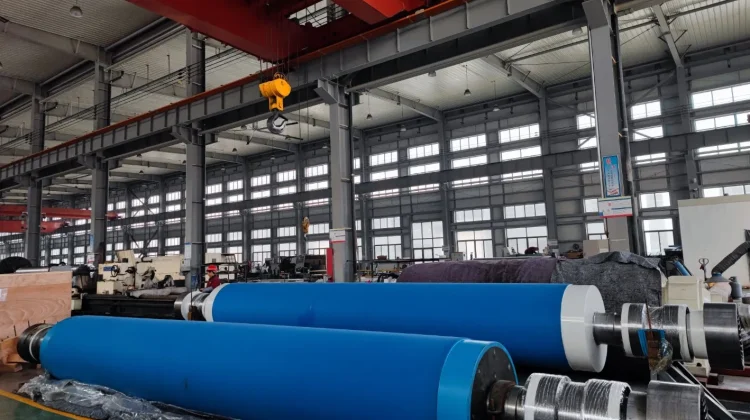
Optimizing Toilet Paper Production with Quality Stone Rollers
In the intricate world of paper manufacturing, particularly when it comes to the delicate process of creating high-quality tissue and toilet paper, every single component plays a pivotal role. Among these vital parts, the stone roller stands out as a fundamental element within the paper machine line. These rollers aren’t just simple cylinders; they are precision-engineered components designed to withstand immense pressure, operate at high speeds, and contribute significantly to the dewatering and finishing processes that are crucial for the final product’s quality and texture. Their importance in the press section cannot be overstated, as they help remove water from the paper web, consolidate the sheet, and prepare it for drying. Without properly functioning stone rollers, achieving the desired strength, softness, and overall quality of toilet paper would be practically impossible. Frankly speaking, their reliable performance is directly linked to the mill’s productivity and the consistency of its output, making them a core asset that demands attention and care throughout its lifecycle. It’s worth noting that the specific demands placed on a Stone Roller for Toilet Paper & Paper Mill Machinery (Spare Part) can differ slightly from those used in other types of paper production, primarily due to the unique properties desired in tissue, such as bulk and absorbency, which are influenced by the pressing stage.
The Vital Role of Stone Rollers in Toilet Paper Manufacturing
Understanding the specific function of stone rollers within the paper machine is key to appreciating their value. In the context of toilet paper manufacturing, these rollers are typically situated in the press section, a critical phase where mechanical pressure is applied to the wet paper web to squeeze out water. While heat drying accounts for a significant portion of water removal, the press section is by far the most energy-efficient method. Stone rollers, often used in conjunction with felt or other types of rollers, form nip points where the paper web passes through under tremendous force. This pressing action reduces the water content from perhaps 80% down to 50-60% or even less, dramatically lessening the load on the subsequent, energy-intensive drying section. Beyond simple dewatering, the configuration and condition of the stone roller also influence the density and surface characteristics of the final paper. The smooth, hard surface of a well-maintained stone roller ensures uniform pressure distribution across the web width, which is essential for preventing weak spots, inconsistencies, and web breaks – issues that can bring the entire production line to a halt. Have you ever considered just how much precision is required to apply tons of pressure evenly across a width of several meters at high speeds? It’s a testament to the engineering involved. This process is fundamental to achieving the desired caliper (thickness) and feel of the toilet paper, making the stone roller an indispensable piece of the machinery.
Understanding the Press Section’s Core Component
The press section of a paper machine, especially one configured for tissue production, is a complex assembly of rollers, felts, and auxiliary systems designed to maximize water removal while minimizing damage or disruption to the fragile paper web. At the heart of many such press configurations is at least one stone roller, often positioned strategically within a press nip. The stone roller’s inherent hardness and resistance to deflection under load make it ideal for creating a stable, high-pressure nip. Different press designs exist, such as straight-through presses, suction presses, or shoe presses, and the stone roller can be integrated into various layouts. For instance, in a conventional two-roll press, a stone roll might be paired with a rubber-covered roll. The interaction between the roller surfaces and the felt, which carries the paper web, is meticulously calibrated. The porosity and surface finish of the stone roll are critical factors; they must facilitate the efficient transfer of water from the felt into the felt itself or into vacuum systems, preventing rewetting of the paper web after the nip. A worn or damaged stone roller can lead to uneven pressing, poor dewatering, increased energy consumption in the dryer section, and ultimately, compromised product quality or reduced machine speed. Maintaining the perfect profile and surface of this component is paramount for operational efficiency and product consistency.
Materials Science Behind Durable Stone Rollers
The composition of stone rollers used in paper mill machinery is a fascinating intersection of material science and engineering requirements. Traditionally, these rollers were indeed made from natural stone, such as granite, known for its hardness and density. However, modern technology has introduced composite materials that offer enhanced properties specifically tailored for the rigorous demands of paper production. These composites often involve synthetic materials combined with reinforcing fibers or binders, resulting in rollers that can be lighter, stronger, more resistant to chemicals used in the process, and less prone to cracking than traditional natural stone. The selection of the material depends heavily on the specific application within the paper machine, the type of paper being produced, the operating speed, and the chemical environment. Properties like hardness are crucial for resisting wear and maintaining the roller’s profile over time. Chemical resistance is vital because the process water in a paper mill can contain various chemicals that could degrade certain materials. Porosity is also a key consideration, influencing how effectively water is removed from the felt and prevented from being reabsorbed by the paper web. Achieving the right balance of these properties through careful material selection and manufacturing processes is what gives a high-quality stone roller its longevity and performance characteristics. It’s a delicate balance, striving for durability without sacrificing the necessary surface properties required for the intricate dewatering process.
Selecting the Right Composition for Performance
Choosing the appropriate material composition for a stone roller is not a ‘one size fits all’ situation. Paper mills operate under varying conditions, producing different grades of paper (though here we focus on tissue), and utilizing diverse chemical additives. Therefore, the material specification for a roller must be carefully matched to its intended service. Factors such as operating temperature, pH levels of the process water, potential for abrasive particles in the stock, and the required linear pressure in the press nip all influence the ideal material choice. Modern composite stone rollers can be engineered to offer superior resistance to specific forms of wear or chemical attack compared to natural stone. Suppliers often provide technical data detailing the physical and chemical properties of their roller materials, helping mill operators make informed decisions. Consulting with material experts or experienced roller manufacturers is often advisable to ensure that the selected roller material will perform optimally and provide a long service life in the specific mill environment. Over time, advancements in polymer technology and composite manufacturing continue to push the boundaries of roller performance, offering solutions that can handle higher speeds, greater loads, and more aggressive process conditions, directly contributing to improved efficiency and reduced downtime in the paper making process.
Maintaining Peak Performance: Care for Your Stone Rollers
Even the most robust stone roller requires diligent maintenance to deliver consistent performance throughout its lifespan. The operational environment within a paper mill is harsh, involving constant exposure to water, chemicals, pressure, and friction. Regular inspection is paramount; mill personnel should routinely check for signs of wear, pitting, cracks, or changes in the roller’s surface profile. The presence of hard particles in the paper stock can cause abrasion, gradually altering the roller’s surface and affecting its ability to press evenly. Chemical reactions or prolonged exposure to aggressive substances can also degrade the material over time. Grinding or profiling is a common maintenance procedure where a thin layer is removed from the roller surface to restore its cylindrical shape and smooth finish. This needs to be done with precision by skilled technicians using specialized equipment. Proper cleaning is also essential to prevent the build-up of paper fibers, pitch, or chemical residues on the surface, which can lead to uneven pressing, marking the paper web, or damaging the roller or felt. Implementing a proactive maintenance of stone rollers in paper mills program, including scheduled inspections, cleaning, and profiling, is infinitely more cost-effective than dealing with the consequences of roller failure, such as emergency shutdowns, lost production, and potentially damaged associated equipment. Preventative care truly pays off in the long run for such critical components.
Proactive Inspection and Common Issues
What should a maintenance team look for during routine inspections of stone rollers in a paper machine? Beyond obvious physical damage like chips or cracks, subtle signs can indicate impending issues. Uneven wear patterns, often caused by localized pressure variations or abrasive elements, are a major concern. A slight change in the roller’s diameter profile across its width, known as ‘crowning’ or ‘dishing’, can significantly impact nip uniformity and dewatering efficiency. Surface defects such as pitting or scaling can also occur, affecting the roller’s interaction with the felt and paper web. Acoustic testing or non-destructive testing methods can sometimes be used to detect internal flaws that aren’t visible on the surface. Temperature monitoring of roller bearings is also vital, as overheating can indicate lubrication issues or excessive load, potentially leading to catastrophic failure. Interestingly enough, tracking the history of each roller, including its position in the machine, operating hours, and maintenance records, provides valuable data for predicting future maintenance needs and optimizing grinding schedules. Addressing minor issues early through proactive inspection prevents them from escalating into major problems requiring expensive repairs or premature replacement. Ignoring these warning signs is akin to driving a car without ever checking the tires – you know you’re likely heading for trouble down the road.
The Importance of Quality Stone Roller Spare Parts
Despite the best maintenance practices and the inherent durability of modern materials, stone rollers, like all mechanical components subjected to heavy loads and constant use, have a finite operational life. Eventually, wear and tear will necessitate their replacement. This is where the importance of having access to high-quality paper machine spare parts for tissue production becomes critically apparent. Sourcing a replacement Stone Roller for Toilet Paper & Paper Mill Machinery (Spare Part) is not a simple transaction; it’s an investment in the future reliability and performance of the entire paper machine. A sub-standard spare part might initially seem cheaper, but it can lead to a host of problems: shorter service life, inconsistent performance, increased maintenance needs, and even potential damage to other parts of the machine or compromise of the paper quality. Given the long lead times often associated with manufacturing large, precision-engineered rollers, proactive planning for spare parts is essential. Waiting until a roller fails unexpectedly can result in prolonged and costly downtime. Establishing relationships with reputable suppliers who understand the specific requirements of tissue paper production and can deliver parts meeting stringent quality specifications is a key strategic consideration for any paper mill aiming for high efficiency and consistent output.
Sourcing Reliable Components for Paper Machines
When the time comes to replace a worn-out stone roller, the sourcing process for a quality spare part is paramount. Several factors should guide the selection of a supplier and the specific replacement roller. Firstly, technical specifications are non-negotiable; the replacement roller must match or exceed the dimensions, material composition, surface finish, and load capacity requirements of the original part. Precision in manufacturing is critical to ensure proper fitment, balance, and performance at high operating speeds. Secondly, the reputation and expertise of the supplier are vital. Are they experienced in providing selecting stone rollers for high-speed paper machines? Do they have a proven track record of delivering reliable components? Do they offer technical support and potentially even installation assistance or guidance? Lead times for manufacturing custom rollers can be substantial, so planning ahead is crucial. Having a trusted supplier who can meet deadlines and quality standards is invaluable. In my experience, partnering with suppliers who specialize in paper mill machinery components often provides better results than opting for generic manufacturers, as they possess specific knowledge of the industry’s unique demands. Always request detailed specifications and quality assurance documentation for any potential spare part.
Ensuring Future Reliability in Paper Production
In conclusion, the stone roller is a quiet, yet incredibly powerful contributor to the efficiency and quality of toilet paper production. Its role in the dewatering process is foundational, directly impacting energy consumption, machine speed, and the final product’s characteristics. From selecting the right material composition for specific operating conditions to implementing rigorous maintenance protocols, every step taken to care for these essential components directly translates into improved mill performance. Recognizing when a roller has reached the end of its service life and having a strategy in place for sourcing high-quality Stone Roller for Toilet Paper & Paper Mill Machinery (Spare Part) is not just good practice; it’s critical for minimizing downtime and maximizing profitability. Investing in reliable spare parts from trusted manufacturers is an investment in the future reliability of your paper machine. It prevents unexpected failures, ensures consistent product quality, and ultimately safeguards the operational continuity of the mill. Prioritizing the quality of components like stone rollers is a clear path to achieving sustained success in the competitive world of paper manufacturing.
For more detailed information, please visit our official website: Stone Roller for Toilet Paper & Paper Mill Machinery (Spare Part)