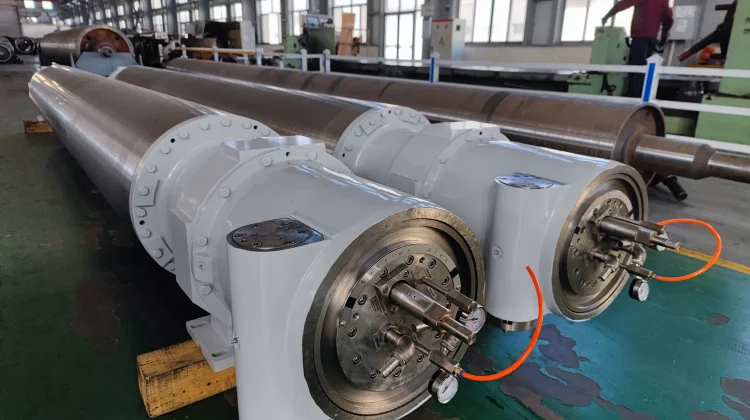
Optimize Recycled Paper Dewatering with Large Diameter Stainless Steel Blind Press Rolls
In the complex world of paper manufacturing, particularly when dealing with recycled fiber furnish, efficiency is paramount. The press section stands as a critical bottleneck where significant energy is consumed, and paper quality is heavily influenced. Effective water removal at this stage is not just about saving energy; it’s fundamentally about strengthening the paper web, reducing breaks, and preparing it for the drying section, which is exponentially more expensive to operate. Historically, press rolls have evolved significantly, moving from simple solid rolls to grooved and suction designs, each aiming to improve dewatering. However, the unique challenges presented by recycled paper—specifically the presence of contaminants, stickies, and variable fiber quality—demand solutions that offer robust performance, corrosion resistance, and efficient water handling. This is precisely where the **Large Diameter Stainless Steel Blind Press Roll for Recycled Paper Machinery** emerges as a cornerstone technology, providing a powerful combination of mechanical strength, chemical resilience, and optimized dewatering capabilities essential for modern recycled paper production lines.
The Strategic Advantage of Large Diameter in Press Rolls
Opting for a large diameter in a press roll isn’t merely a matter of scale; it’s a strategic design choice with profound implications for paper machine performance, especially when processing challenging recycled pulp. A larger diameter roll, when paired with another roll, creates a wider nip. This extended dwell time within the nip allows water more time to flow into the press felt and away from the paper web under pressure. In recycled paper production, where fibers can be less uniform and often carry residual contaminants that hinder dewatering, this increased dwell time is invaluable. It facilitates more efficient water removal, directly contributing to a higher dry content leaving the press section. Furthermore, a wider nip distributes the pressing force over a larger area, resulting in lower linear pressure for a given total force. This is crucial for maintaining web integrity, reducing the risk of crushing or damaging the delicate recycled fiber structure, and ultimately minimizing paper breaks. Frankly speaking, reduced paper breaks translate directly into increased machine uptime and higher overall productivity – a significant factor in the competitive landscape of recycled paper manufacturing.
How Increased Nip Width Impacts Dewatering Efficiency
Let’s delve a little deeper into the mechanics of how that increased nip width, characteristic of a large diameter roll, enhances dewatering. The process relies on transferring water from the paper web into the porous press felt under high pressure. As the paper web and felt pass through the press nip, water is squeezed out. With a wider nip, this squeezing action is sustained for a longer duration as the web and felt travel across the nip’s width. This extended pressure application provides more time for water to migrate from the intricate network of fibers in the paper web into the void volume of the felt. For recycled fiber, which may contain shorter fibers, fillers, and stickies, this extra time is particularly beneficial in overcoming resistance to flow. It allows for a more thorough dewatering process within the press section itself, meaning less water burden is placed on the energy-intensive dryer section downstream. From an operational perspective, achieving a higher dry content post-press can lead to substantial energy savings in drying and potentially allow for increased machine speed, directly contributing to the goal of **optimizing dewatering recycled paper machinery** and boosting profitability.
Why Stainless Steel is Indispensable for Recycled Paper Machinery
The chemical environment within a recycled paper mill is notoriously aggressive. Pulp slurry derived from recycled sources often contains residual chemicals from the original paper production, inks, coatings, and various contaminants introduced during collection and processing. These substances, combined with the necessary process water and additives, create a corrosive cocktail that can wreak havoc on traditional roll materials like cast iron or carbon steel. This is where the selection of stainless steel becomes not just beneficial, but frankly, essential for a **Large Diameter Stainless Steel Blind Press Roll for Recycled Paper Machinery**. Stainless steel, particularly certain grades like duplex or high-alloy austenitics, offers exceptional resistance to corrosion, pitting, and chemical attack. This inherent durability ensures the structural integrity of the roll shell is maintained over extended periods, preventing premature failure or surface degradation that could compromise dewatering efficiency or damage the paper web. It also resists the adhesion of sticky contaminants, which are a perpetual problem in recycled paper lines, making cleaning and maintenance easier and more effective. In my experience, investing in stainless steel for critical components like press rolls in this environment pays dividends in terms of longevity, reliability, and reduced maintenance headaches.
Addressing Corrosive Challenges with Stainless Steel Alloys
The specific grade of stainless steel chosen for a large diameter blind press roll is a critical technical decision. Recycled paper processes can involve varying pH levels, chloride concentrations (from bleach or broke handling), and temperatures, all of which influence corrosion rates. Standard austenitic stainless steels like 304 or 316 might suffice in some less aggressive scenarios, but for many recycled paper applications, especially those dealing with higher levels of contaminants or more demanding deinking processes, more robust alloys are often required. Duplex stainless steels, for instance, offer a combination of high strength and excellent resistance to stress corrosion cracking and pitting, making them well-suited for highly loaded press roll applications in corrosive environments. High-alloy austenitic stainless steels provide even greater resistance to extremely aggressive conditions. Manufacturers carefully select the appropriate stainless steel grade based on the specific process chemistry of the mill. This careful material selection ensures that the large diameter roll maintains its structural integrity and surface finish, which is vital for consistent dewatering and preventing damage to the felt and paper web, thereby extending the operational life and ensuring reliable performance from **stainless steel press rolls for paper mills** handling recycled furnish.
The Efficiency of Blind Drilling for Recycled Pulp Dewatering
The ‘blind’ aspect of the blind press roll refers to a specific pattern of holes drilled partway into the roll shell’s surface. Unlike suction rolls which have holes drilled through the shell and require vacuum to pull water, blind drilled rolls rely solely on the pressure applied in the nip. As the paper web and felt enter the nip, the pressure forces water from the web and felt into these blind drilled holes. The solid land area between the holes provides the necessary pressure to squeeze the water out, while the holes themselves act as temporary reservoirs to accept this displaced water. This design is particularly effective in high-pressure nips created by large diameter rolls. The blind holes efficiently capture water without the need for vacuum, simplifying the press section design and reducing energy consumption associated with vacuum systems. For recycled paper, which can have variable drainage characteristics and contain particles that could potentially plug through-holes in a suction roll, the blind drilled design offers a robust and less maintenance-intensive solution for managing water effectively within the nip, supporting the overall goal of **optimizing dewatering recycled paper machinery**.
Comparing Blind Drilled vs. Other Press Roll Technologies for Recycled Fiber
When considering press roll technology for recycled paper lines, understanding the differences between blind drilled, grooved, and suction rolls is important. Grooved rolls provide channels for water to escape, but their effectiveness can be limited in very wide or high-pressure nips, and grooves can accumulate contaminants. Suction rolls offer powerful water removal via vacuum, but they are mechanically complex, energy-intensive, and the through-holes can be prone to plugging from stickies and fines commonly found in recycled pulp, requiring frequent cleaning and maintenance. Blind drilled rolls, especially those with optimized drilling patterns, offer a compelling balance. They provide efficient water handling in high-pressure, wide nips without the complexity and energy consumption of vacuum. The blind holes are less susceptible to plugging by larger particles compared to through-holes. While they still require cleaning, the maintenance is generally less demanding than that for suction rolls. For large diameter applications in recycled paper mills, the combination of a wide nip for extended dwell time and the effective, robust water handling of blind drilling makes the **Large Diameter Stainless Steel Blind Press Roll for Recycled Paper Machinery** a highly effective choice for achieving optimal dewatering performance with challenging fiber sources.
Design Considerations for Optimal Performance with Recycled Stock
Designing a large diameter stainless steel blind press roll specifically for recycled paper machinery involves careful consideration of several critical factors beyond just the material and drilling pattern. The optimal drilling pattern itself—including hole diameter, depth, angle, and spacing—must be engineered based on the specific speed, pressure, and furnish characteristics of the paper machine. An incorrect pattern can lead to poor dewatering, vibration, or even damage to the web or felt. Furthermore, the roll shell’s thickness and internal ribbing must be sufficient to withstand the immense pressures encountered in the nip of a large diameter roll while maintaining structural integrity and minimizing deflection. Roll crown profile is another vital aspect; it must be precisely calculated to ensure uniform pressure across the entire width of the paper web, compensating for the elastic deformation of the rolls under load. This uniform pressure is essential for consistent dewatering and avoiding streaks or caliper variations in the finished paper. Precision balancing of the finished roll is also non-negotiable for high-speed operation, preventing vibrations that could negatively impact dewatering, web stability, and component lifespan. Addressing these design nuances is key to manufacturing a roll that truly performs optimally with recycled fiber.
Manufacturing Precision and Quality Assurance
The manufacturing process for a **Large Diameter Stainless Steel Blind Press Roll for Recycled Paper Machinery** requires specialized equipment and expertise. Machining large stainless steel forgings or castings to the required dimensions and surface finish is a significant undertaking. The blind drilling operation itself demands high-precision drilling machines capable of executing the intricate pattern accurately and consistently across the entire roll surface. Maintaining tight tolerances on hole depth, angle, and spacing is crucial for the roll’s hydraulic function and mechanical balance. After drilling, the roll surface requires finishing to a specific roughness, often involving grinding and polishing, to ensure optimal interaction with the press felt and paper web. Finally, the roll must undergo rigorous quality control checks, including dimensional inspection, non-destructive testing of the stainless steel material, verification of the drilling pattern, dynamic balancing, and hydrostatic testing to confirm structural integrity. Given the scale and complexity of these components, partnering with a manufacturer possessing proven capabilities in producing **large diameter stainless steel blind press rolls** is essential to guarantee reliability and performance in demanding recycled paper mill environments.
Operation and Maintenance Strategies for Longevity and Efficiency
Once installed, the performance and lifespan of a large diameter stainless steel blind press roll are heavily influenced by operational practices and a robust maintenance program. Monitoring roll condition regularly is vital. This includes inspecting the roll surface for wear, damage, or contaminant buildup. Cleaning procedures are particularly critical in recycled paper applications due to the prevalence of stickies and other deposits. Effective high-pressure showering systems, often utilizing hot water or chemical additives, are necessary to keep the blind holes clear and the roll surface clean. Regular inspection and cleaning of showers are equally important. Furthermore, monitoring bearing temperature and vibration can provide early warnings of potential issues. While stainless steel resists corrosion, the roll surface will eventually require reconditioning due to wear from the felt or paper web. Establishing a schedule for periodic grinding to restore the crown profile and surface finish is crucial for maintaining dewatering efficiency and extending the roll’s operational life. Proactive maintenance, including timely regrinding and bearing replacement, is key to ensuring that these significant investments continue to contribute to **improving paper machine efficiency recycled furnish**.
Optimizing Dewatering Performance Through Roll Management
Effective management of your large diameter stainless steel blind press roll goes beyond just basic maintenance; it involves optimizing its performance within the context of your specific recycled paper machine setup. This includes carefully selecting the press felt type and conditioning program to work in harmony with the blind drilled surface. Monitoring key operational parameters like nip pressure, machine speed, and sheet dry content exiting the press section allows operators to identify opportunities for optimization or detect deviations from expected performance. Data analysis of these parameters over time can help predict when maintenance, such as regrinding or intense cleaning, might be necessary to prevent performance degradation. Collaborating with felt suppliers and roll manufacturers can provide valuable insights into best practices for operating and maintaining these specialized rolls for maximum dewatering efficiency with challenging furnishes. Have you analyzed your press section performance metrics lately? Ensuring your **large diameter stainless steel blind press rolls** are operating at their peak condition is fundamental to maximizing water removal and minimizing drying costs in recycled paper production.
Measuring the Impact: Performance Metrics and Return on Investment
Justifying the investment in high-quality components like a large diameter stainless steel blind press roll requires demonstrating tangible benefits. Key performance indicators (KPIs) for the press section provide the necessary data. The most direct metric is the sheet dry content exiting the press section – even a small percentage increase here translates to significant energy savings in drying. Reduced paper breaks, another critical KPI, directly impacts machine uptime and throughput. Energy consumption specifically related to the press section and subsequent drying is also a clear indicator of efficiency improvements. While the initial cost of a large diameter stainless steel blind press roll might be higher than alternative materials or designs, its durability, corrosion resistance, reduced maintenance needs, and crucially, its superior dewatering capability in demanding recycled paper applications often lead to a compelling return on investment (ROI). The cumulative savings from reduced energy usage, increased production uptime, and extended component lifespan can quickly offset the initial expense. Frankly speaking, the long-term operational advantages make these rolls a financially sound decision for mills focused on efficient recycled paper production.
Future Trends and Innovations in Press Roll Technology
The evolution of press roll technology continues, driven by the ongoing need for greater efficiency, reliability, and adaptability to challenging furnishes like recycled fiber. Future trends for large diameter stainless steel blind press rolls may include advanced surface treatments or coatings designed to further reduce sticky accumulation and enhance wear resistance. Development in stainless steel alloys could lead to even greater corrosion resistance or strength-to-weight ratios. Furthermore, advancements in monitoring technology, such as integrated sensors for measuring temperature, vibration, or even nip pressure profiles in real-time, could allow for more precise operation and predictive maintenance. Intelligent control systems could potentially adjust press parameters dynamically based on online measurements of sheet properties. These innovations aim to further optimize the performance of **large diameter stainless steel blind press rolls**, pushing the boundaries of dewatering efficiency and operational reliability in the demanding environment of recycled paper machinery. It’s worth noting how continuous innovation in these critical components supports the broader goals of sustainability and efficiency in the paper industry.
Conclusion: Securing Efficiency and Reliability in Recycled Paper Production
The press section remains a cornerstone of paper machine efficiency, particularly when processing recycled fiber furnish with its inherent complexities and contaminants. The selection of robust, high-performance components is not a luxury but a necessity. As we’ve explored, the **Large Diameter Stainless Steel Blind Press Roll for Recycled Paper Machinery** offers a powerful combination of features specifically designed to meet these challenges head-on. The large diameter creates a wider, more effective dewatering nip, stainless steel provides essential corrosion resistance against aggressive process chemistry, and blind drilling offers reliable, vacuum-free water handling. Together, these elements contribute significantly to optimizing dewatering efficiency, reducing energy consumption, minimizing paper breaks, and extending the operational life of critical components. Investing in high-quality large diameter stainless steel blind press rolls is a strategic decision that pays dividends in terms of reliability, productivity, and profitability in the demanding world of recycled paper manufacturing. To ensure you are leveraging the best technology for your specific recycled paper production needs, exploring high-quality roll solutions is a crucial next step. For more detailed information, please visit our official website: Large Diameter Stainless Steel Blind Press Roll for Recycled Paper Machinery