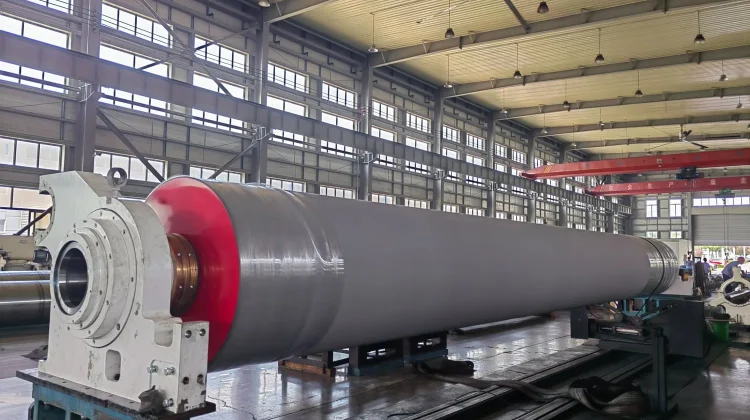
Critical Role of Paper Mill Rolls Explained
In the intricate world of pulp and paper manufacturing, achieving the desired quality, consistency, and efficiency hinges significantly on a seemingly simple component: the paper mill rolls. These robust cylindrical structures are the workhorses of the paper machine, guiding, pressing, forming, and drying the paper web through various stages. Without precisely engineered and well-maintained rolls, the entire process would grind to a halt, resulting in wasted resources and subpar output. Understanding their function, types, and the critical need for proper care is paramount for anyone involved in this industry, from machine operators to procurement specialists. It’s frankly speaking, an area that demands attention.
The Unsung Heroes: Function and Types of Paper Mill Rolls
Have you ever wondered about the journey of a single sheet of paper from pulp to finished product? It’s a complex path involving numerous mechanical actions, many of which are facilitated by paper mill rolls. These rolls aren’t just passive guides; they apply pressure, remove water, impart surface characteristics, and transport the fragile web at high speeds. Different stages of the paper machine require specialized rolls, each designed for a specific task. For instance, forming rolls help dewater the pulp slurry on the forming fabric, press rolls squeeze out significant amounts of water, dryer rolls use heat to evaporate moisture, and calendar rolls smooth the surface and control thickness. Each type of roll operates under unique conditions, facing varying degrees of load, temperature, and chemical exposure, demanding specific material compositions and surface properties. Choosing the right rolls for each position is a decision that directly impacts machine performance and paper quality.
Understanding the Demands on Forming and Press Section Rolls
The journey begins in the forming section, where the initial web is created. Here, forming rolls and couch rolls play a crucial role in the first major dewatering steps. These rolls are often subjected to abrasive conditions due to the nature of the pulp and the forming fabric. Moving into the press section, the demands escalate dramatically. Press rolls are designed to apply immense pressure, sometimes thousands of pounds per linear inch, to mechanically squeeze water from the web. This is a high-stress environment. Roll covers, made from specialized rubber, polyurethane, or composite materials, are essential here to prevent crushing the web, improve dewatering efficiency, and provide grip. The materials used for these rolls and their covers must withstand continuous pressure, heat generated by friction, and various papermaking chemicals. Proper crown (a slightly convex profile) is also vital on press rolls to ensure even pressure distribution across the wide web width. Without the correct setup here, issues like uneven moisture profiles and sheet breaks become common problems, severely impacting production speed and quality.
Materials and Coatings: The Foundation of Roll Performance
The performance and longevity of paper mill rolls are heavily dependent on the materials they are made from and the coatings applied to their surfaces. The core of a roll is typically constructed from steel or cast iron, chosen for its strength and stability under load. However, the surface is where the magic, or rather, the engineering, happens. Roll covers are critical for preventing sheet sticking, improving dewatering, resisting wear, and providing the necessary grip. Materials like rubber, polyurethane, ceramics, and various composite materials are used, each offering different properties in terms of hardness, elasticity, temperature resistance, and chemical inertness. For dryer rolls, materials that facilitate heat transfer, like cast iron or steel alloys, are paramount, often with polished or coated surfaces to prevent sticking. Calendar rolls might use chilled cast iron for hardness and polishing ability. Interestingly enough, advancements in coating technology have led to specialized surfaces that enhance release properties, improve wear resistance, and even reduce energy consumption. Selecting the optimal material and coating combination for each specific application within the paper machine is a complex task requiring deep knowledge of the process and material science. It’s a decision that pays significant dividends in terms of efficiency and product quality.
Specialized Rolls in the Dryer and Calender Sections
Once the paper web leaves the press section, it still contains significant moisture and needs to be dried. This is the realm of the dryer section, dominated by numerous large-diameter dryer rolls. These rolls are typically steam-heated and are responsible for evaporating the remaining water content, often bringing the moisture down to a desired level, usually around 5-8%. The surfaces of dryer rolls must be smooth and corrosion-resistant to prevent the paper from sticking as it dries under heat and tension. Following drying, the paper often passes through the calender section. Calendar rolls are used to compact the paper, control its thickness, and smooth or gloss its surface. These rolls are typically hard, often made of chilled iron, and arranged in stacks. Nip pressure and temperature in the calender stack are carefully controlled to achieve the desired finish and caliper. Specialized calendar rolls, like soft nip rolls with resilient covers, offer more flexibility in controlling surface properties. The unique challenges in these sections – high temperatures, surface interaction, and the need for precise control – necessitate specific roll designs and material choices distinct from the wet end of the machine.
Maintaining Peak Performance: Inspection and Maintenance of Paper Mill Rolls
Given the constant stress, high speeds, and challenging environments they operate in, paper mill rolls require rigorous and routine maintenance to ensure peak performance and prevent costly downtime. A comprehensive maintenance program involves regular inspection, cleaning, grinding, and sometimes, recovering or replacing roll covers. Inspections look for signs of wear, damage, corrosion, or cover deterioration. Surface irregularities, even minor ones, can lead to uneven pressure, poor dewatering, surface defects in the paper, or even sheet breaks. Grinding (or regrinding) is a critical process to restore the correct profile (crown) and surface finish of the rolls, compensating for wear and preventing vibration issues. For rolls with covers, timely regrinding and eventual replacement of the cover are essential to maintain performance. Neglecting roll maintenance is a surefire way to introduce inefficiency, reduce paper quality, and significantly increase the risk of unplanned outages. Investing in proactive maintenance is, to be honest, one of the best investments a paper mill can make to protect its productivity and profitability. It’s not just about fixing problems; it’s about preventing them before they occur.
Addressing Common Issues and Extending Roll Lifespan
Even with diligent maintenance, paper mill rolls face common issues throughout their operational life. These can include wear and abrasion, chemical attack on covers, heat cracking, vibration, and profile changes (losing the designed crown). Addressing these issues promptly is crucial. For instance, wear can be mitigated by using more abrasion-resistant cover materials or optimizing cleaning procedures. Chemical attack requires covers with higher chemical resistance suitable for the process environment. Vibration often indicates imbalance or improper crowning and requires careful inspection and potentially dynamic balancing. Profile changes necessitate regrinding to restore the correct shape. Extending roll lifespan involves a combination of selecting appropriate materials for the specific application, implementing a robust preventative maintenance schedule, ensuring proper machine alignment, and carefully monitoring roll condition through techniques like non-destructive testing. Furthermore, understanding the root cause of frequent issues, such as uneven wear patterns, can lead to process adjustments or material changes that significantly improve roll longevity. It’s a continuous cycle of monitoring, analysis, and action aimed at maximizing the return on investment in these critical components.
The Impact of Roll Condition on Paper Quality and Machine Efficiency
The direct link between the condition of paper mill rolls and the quality of the final product, as well as overall machine efficiency, cannot be overstated. A roll with incorrect crowning will result in uneven pressure application, leading to variations in moisture profile, caliper, and density across the web. This can cause issues downstream in winding, converting, and printing, and ultimately, affect the customer’s perception of quality. Surface imperfections on rolls, whether from wear, damage, or improper cleaning, can transfer marks or defects onto the paper sheet. Furthermore, rolls in poor condition can lead to increased sheet breaks, forcing machine slowdowns or shutdowns, drastically reducing production output and increasing waste. Worn or improperly maintained rolls can also consume more energy due to increased friction or suboptimal dewatering. Frankly speaking, the performance of every single roll in the paper machine chain contributes significantly to the overall operational efficiency and the ability to produce high-quality paper consistently. Investing in the right rolls and keeping them in optimal condition is not an option; it’s a necessity for competitive papermaking.
Technological Advancements in Paper Mill Roll Technology
The field of paper mill rolls isn’t stagnant; it’s constantly evolving with technological advancements aimed at improving performance, increasing lifespan, and reducing maintenance requirements. Innovations in roll cover materials, including advanced polymers and composite materials, offer enhanced wear resistance, chemical resistance, and release properties. These new covers can operate at higher temperatures and pressures, contributing to faster machine speeds and improved dewatering. Dynamic balancing techniques have become more sophisticated, reducing vibration and extending bearing life. Advanced monitoring systems, using sensors and data analytics, can track roll temperature, vibration, and even predicted wear, allowing for more precise and predictive maintenance. Furthermore, improvements in grinding and surface finishing technologies enable tighter tolerances and more consistent roll profiles. Roll manufacturers are also developing lighter, stronger roll designs that can handle higher loads while potentially reducing energy consumption. These advancements represent significant opportunities for paper mills to upgrade their machines, boost performance, and stay competitive in a demanding market. Keeping abreast of these innovations is key to optimizing production processes.
Choosing the Right Partner for Your Paper Mill Roll Needs
Given the complexity and critical nature of paper mill rolls, selecting the right supplier or partner is as important as choosing the rolls themselves. A good partner offers not just a product, but also expertise and support. They should be able to help you assess your specific machine requirements, recommend the optimal roll types, materials, and covers for each position, and provide valuable insights into maintenance best practices. Look for a partner with a proven track record, deep industry knowledge, and a commitment to quality and service. They should offer comprehensive services, including roll manufacturing, grinding, balancing, cover application, and potentially even advanced diagnostics. A partner who understands the nuances of your specific paper grades and machine configuration can provide tailored solutions that genuinely improve your operational efficiency and product quality. This partnership extends beyond the initial purchase; ongoing technical support and timely service are crucial for maximizing the value and performance of your paper mill rolls throughout their life cycle. It’s an important decision that impacts your bottom line directly.
In conclusion, paper mill rolls are far more than just cylinders; they are precision-engineered components that are absolutely fundamental to the papermaking process. Their design, materials, and condition directly influence everything from dewatering efficiency and energy consumption to sheet quality and machine uptime. Understanding the diverse types of rolls, the specific demands of each section, and the importance of proactive maintenance is vital for operational success. As technology continues to advance, so too do the capabilities of these essential machine parts. By investing in high-quality paper mill rolls and partnering with experts who understand their critical role, paper mills can significantly enhance their productivity, improve the quality of their product, and ensure long-term profitability in a competitive landscape. What steps are you taking today to ensure your rolls are performing at their peak?
For more detailed information, please visit our official website: paper mill rolls