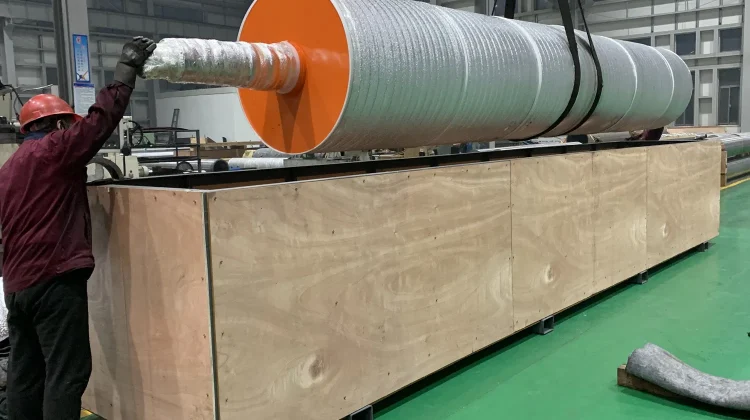
Optimizing Paper Machine Press Rolls
In the complex and intricate world of paper manufacturing, every component plays a vital role in achieving the desired quality and efficiency. Among these, the paper machine press roll stands out as a truly critical element. It’s not just a rotating cylinder; it’s a precision tool engineered to perform one of the most important steps in the papermaking process: dewatering the newly formed paper web. Getting the press section right can significantly impact energy consumption, machine speed, and ultimately, the strength and finish of the final paper product. Frankly speaking, overlooking the importance of these rolls, their design, operation, and maintenance, is simply not an option for mills striving for excellence.
The Crucial Function of Press Rolls in Dewatering
Let’s talk about what these rolls actually do. Following the forming section, where the paper web is initially created from a pulp slurry, the web still contains a substantial amount of water – often upwards of 80% or even 90%. The press section, driven by various types of paper machine press rolls, is tasked with mechanically removing as much of this water as possible before the web enters the dryer section. This mechanical dewatering is far more energy-efficient than thermal drying, making the press section performance directly linked to operational costs. The rolls create a ‘nip’ – a line of contact under pressure – through which the web passes. As the web is squeezed, water is forced out of the fiber structure. The efficiency of this water removal is influenced by factors like nip pressure, dwell time in the nip, roll surface properties, and water drainage paths.
Understanding Different Press Roll Designs
The design of press rolls has evolved significantly over the years to meet the increasing demands for speed, efficiency, and paper quality. Early designs included simple plain press rolls, but these had limitations in water removal and could lead to crushing of the web. The introduction of the suction press roll was a major leap forward. These rolls feature drilled shells with an internal suction box, pulling water away from the web and into the roll, thus preventing rewetting and improving dewatering. Grooved rolls and blind-drilled rolls offered alternative strategies for providing drainage paths for the water within the nip. More recently, the hydraulic shoe press has become prominent, offering a much longer nip and higher pressures, leading to exceptional dewatering and significant energy savings in the drying section. Choosing the right type of press roll depends heavily on the grade of paper being produced, machine speed, and desired sheet properties.
Materials, Covers, and Their Impact on Performance
The performance and longevity of a press roll are intrinsically linked to the materials used in its construction and its cover. Roll shells are typically made from cast iron, ductile iron, or fabricated steel, chosen for their strength and rigidity under immense pressure. However, the surface, or cover, is where much of the magic happens – and where wear and tear are most evident. Historically, covers were primarily rubber, but modern paper machines utilize advanced polymer composites, polyurethane, and even ceramic coatings. These materials are selected based on their hardness, resilience, chemical resistance, heat resistance, and friction properties. A cover’s porosity, hardness, and groove or drilling pattern are engineered to optimize water removal, minimize web slippage, and resist buildup. The right cover material can significantly extend run times between grinds or changes and improve sheet consistency.
Maintaining Optimal Operation and Lifespan
Proper operation and diligent maintenance are absolutely non-negotiable for maximizing the efficiency and lifespan of a paper machine press roll. Regular inspections are crucial to detect early signs of wear, damage, or cover degradation. Monitoring nip uniformity and pressure profiles ensures even dewatering across the web width. Roll grinding or resurfacing is periodically required to restore the crown (the slightly tapered shape designed to counteract deflection under load) and ensure a smooth, optimal surface for the nip. For suction rolls, maintaining the vacuum system and ensuring the cleanliness of drill holes is paramount. Lubrication of bearings and proper alignment are also fundamental maintenance tasks. Ignoring these aspects can lead to uneven pressing, sheet quality issues, increased energy consumption, and potentially costly roll failures. In my experience, proactive maintenance programs pay for themselves many times over.
Addressing Common Issues and Troubleshooting
Even with the best maintenance practices, press rolls can encounter issues. Common problems include uneven cover wear, which leads to non-uniform dewatering and variable sheet moisture profiles; roll deflection beyond design limits, impacting nip uniformity; cracking or damage to the cover or shell; and buildup of contaminants on the roll surface. Troubleshooting requires a systematic approach. For uneven wear, the cause could be mechanical (alignment issues, bearing problems) or process-related (uneven web moisture, localized pressure variations). Cracking might indicate thermal stress or mechanical overload. Monitoring key performance indicators like roll surface temperature, vibration levels, and power consumption can often provide early warnings. Understanding the root cause of an issue is critical before attempting a solution. Have you ever faced unexpected press section issues and wondered about the underlying cause?
Innovations and Advanced Technologies in Pressing
The quest for higher machine speeds, improved paper quality, and reduced energy costs has driven continuous innovation in press roll technology. As mentioned earlier, the rise of the shoe press technology has revolutionized dewatering in many grades. These systems replace a conventional roll nip with a long, hydrostatic shoe pressed against a counter roll, dramatically increasing nip dwell time and pressure. This leads to significantly higher dryness entering the dryer section, often allowing for reduced dryer length or increased machine speed. Other advancements include specialized roll covers with unique surface textures or materials for specific paper grades, advanced monitoring systems using sensors to track temperature, pressure, and vibration in real-time, and sophisticated control systems for optimizing nip loading and crown control. These technologies represent significant investments but offer substantial returns in efficiency and product quality.
Selecting the Right Roll for Your Application
Choosing the appropriate type of press roll, cover material, and internal design (like drilling pattern or shoe profile) is a critical decision during machine design or rebuilds. This isn’t a one-size-fits-all scenario. The ideal configuration depends on several factors: the grade of paper being produced (e.g., linerboard vs. fine paper vs. tissue), the desired machine speed, the target sheet dryness after the press section, required sheet properties (bulk, smoothness, strength), and operational considerations like required run time and maintenance capabilities. Consulting with experts who understand the nuances of different roll types and cover technologies is essential to make an informed decision that will yield the best long-term performance and return on investment. Selecting the right paper machine press roll is a strategic choice that impacts the entire downstream process.
Ensuring Peak Performance Through Expert Support
Operating a paper machine press section at peak efficiency requires not only high-quality components but also expertise in their application, operation, and maintenance. Problems with press rolls can be complex, often stemming from a combination of mechanical, operational, and material factors. Identifying the root cause of issues like vibration, uneven wear, or poor dewatering requires specialized knowledge and diagnostic tools. This is where partnering with experienced professionals can make a significant difference. Experts can provide valuable insights into optimizing nip parameters, recommending appropriate roll covers for specific challenges, developing effective maintenance schedules, and troubleshooting difficult problems. Investing in this kind of support helps ensure that your press rolls are performing optimally, contributing directly to energy savings, increased production, and consistent product quality. What challenges are you currently facing with your press section that might benefit from expert analysis?
In conclusion, the paper machine press roll is an indispensable part of the papermaking process, central to efficient dewatering and overall machine performance. From traditional plain rolls to advanced shoe presses, the technology continues to evolve, offering new possibilities for efficiency and quality. Understanding the function, types, materials, and maintenance requirements is key to unlocking the full potential of your press section. Proactive care and expert support are vital in overcoming common challenges and ensuring smooth, productive operations. By focusing on these critical components, paper mills can achieve higher speeds, reduce energy consumption, and produce better paper.
For more detailed information, please visit our official website: paper machine press roll