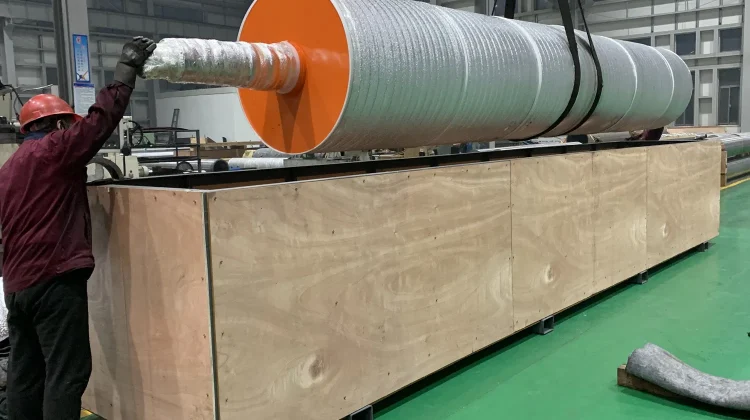
In the demanding world of paper production, every component plays a critical role in ensuring efficiency, quality, and profitability. Among these, the paper mill rolls stand out as indispensable elements that directly impact the final product and the operational lifespan of the machinery. These rolls are subjected to immense pressures, high temperatures, and constant wear, making their design, manufacture, and maintenance absolutely crucial. Therefore, selecting the right partners in the supply chain, specifically skilled paper mill rolls manufacturers, is not merely a purchasing decision; it’s a strategic investment in your mill’s future performance and reliability. The quality of the rolls dictates everything from sheet formation and dewatering to drying and finishing, ultimately influencing paper quality and production speed. To be honest, subpar rolls can lead to frequent downtime, increased maintenance costs, and inconsistent product quality, all of which can significantly erode profit margins. Finding manufacturers who understand the specific challenges of paper production and can deliver rolls engineered for performance and durability is paramount. It’s about securing components that can withstand the rigors of continuous operation while contributing to optimal machine efficiency. This introductory section sets the stage for understanding the vital role these manufacturers play and why choosing wisely is so important for any paper mill aiming for peak operational excellence and consistent product quality in a competitive market. Let’s delve deeper into what defines a leading manufacturer in this specialized field.
Understanding the Diverse World of Paper Machine Rolls
Paper machines utilize a complex array of rolls, each designed for a specific function within the papermaking process. From the forming section where the pulp slurry is initially drained, through the press section that removes water via mechanical pressure, to the dryer section utilizing heat, and finally the calendar and reel sections for finishing and winding, different types of rolls are employed. Forming rolls, often covered with specialized materials, help in the initial drainage and formation of the paper web. Press rolls, which can be made of granite, rubber, or composite materials, work in pairs under tremendous load to squeeze water out of the sheet, a critical step for energy efficiency. Dryer rolls, typically large heated cylinders made of cast iron, remove the remaining moisture through evaporation. Calendar rolls, found in the finishing section, are used to smooth and gloss the paper surface. Each type requires distinct materials, surface finishes, and internal structures to perform its task effectively and withstand the unique stresses of its environment. The complexity and variety mean that paper mill rolls manufacturers must possess a deep understanding of the entire papermaking process and the specific demands placed on each roll type. They need expertise not only in metallurgy and engineering but also in surface science, coating technologies, and even pneumatics and hydraulics for systems like nip control. This comprehensive knowledge is what separates a general machinist from a specialized paper roll manufacturer. Have you ever considered just how many different rolls are involved in taking a liquid pulp mixture all the way to a finished paper roll? It’s a testament to the intricate engineering required at every stage.
What Distinguishes Premier Paper Mill Roll Manufacturers?
Choosing a manufacturer for components as critical as paper mill rolls requires careful consideration beyond just price. Leading paper mill rolls manufacturers are distinguished by several key factors that speak to their capability and reliability. Firstly, their engineering expertise is second to none. This includes not just the ability to machine rolls to precise tolerances but also deep knowledge of materials science, stress analysis, and thermal dynamics relevant to the papermaking environment. They understand how different alloys, coatings, and composite materials will perform under specific operational conditions—temperature, pressure, speed, and chemical exposure. Secondly, their manufacturing facilities are equipped with state-of-the-art machinery for processes like precision grinding, dynamic balancing, and advanced coating applications. Producing a paper roll isn’t just about shaping metal; it’s about achieving microscopic precision, ensuring perfect balance at high speeds to prevent vibration, and applying surfaces that enhance dewatering, release, or finish characteristics. Quality control is another non-negotiable aspect. Top manufacturers implement rigorous testing protocols at every stage, from raw material inspection to final dimension checks and performance simulations. They invest heavily in technology that allows for non-destructive testing, surface analysis, and ultra-precise measurements. Frankly speaking, settling for a manufacturer without these capabilities is a gamble you simply cannot afford in a high-volume, high-speed operation like a paper mill. It’s about partnering with an organization that views roll manufacturing as a blend of science, engineering, and craftsmanship.
The Crucial Role of Custom Engineering and Design
While standard roll designs exist, the reality is that every paper machine is unique, often modified over time, and operates under specific conditions influenced by the type of paper being produced, raw materials used, and desired output characteristics. This is where the ability of paper mill rolls manufacturers to provide custom engineering becomes invaluable. A top manufacturer doesn’t just build rolls; they work with mills to design rolls that are optimized for their specific machine configurations and operational goals. This might involve developing unique roll crowns to ensure even pressure distribution across the web, selecting specialized coatings to improve release properties or wear resistance, or engineering rolls with specific internal cooling or heating capabilities. The process often begins with a thorough analysis of the mill’s current setup, identifying bottlenecks or areas for improvement related to roll performance. Manufacturers with strong R&D capabilities can innovate and propose solutions that might not have been previously considered, leveraging the latest advancements in materials and design. This bespoke approach is particularly important for critical applications or when upgrading older equipment. For example, integrating advanced composites into rolls can reduce weight and inertia, allowing for higher speeds and lower energy consumption. It’s not just about replacing a worn part; it’s about installing a component that is designed to enhance overall machine performance. Finding a manufacturer who excels in offering custom paper machine rolls is a strategic advantage that can lead to significant improvements in efficiency and product quality.
Materials and Surface Technologies in Roll Manufacturing
The performance and lifespan of a paper mill roll are intrinsically linked to the materials used in its construction and the surface technologies applied. Reputable paper mill rolls manufacturers are experts in selecting and applying the right materials for each roll position and function. For roll cores, materials like high-grade cast iron or steel alloys are chosen for their strength, rigidity, and durability under load. However, the surface is where much of the critical interaction with the paper web and machine environment occurs. Rubber covers, for instance, are engineered with specific hardness, elasticity, and chemical resistance properties for press rolls to optimize dewatering and prevent sheet sticking. Composite covers offer advantages in terms of weight reduction, corrosion resistance, and the ability to incorporate specific surface properties. Hard coatings, such as tungsten carbide or ceramics, applied through processes like thermal spraying, provide exceptional wear resistance for rolls exposed to abrasive fillers or high slip. These advanced surface technologies are not simply applied; they require careful process control to ensure optimal adhesion, uniform thickness, and the desired surface finish. The choice of material and surface treatment depends entirely on the roll’s function—whether it needs high grip, smooth release, resistance to wear, or heat transfer capabilities. A manufacturer’s expertise in this area is a direct indicator of the quality and performance you can expect from their rolls. Interestingly enough, advancements in nanotechnologies and polymer science continue to push the boundaries of what’s possible with roll covers and coatings, offering new avenues for improving performance and extending service life.
The Importance of Comprehensive After-Sales Services
The relationship with a paper mill roll manufacturer shouldn’t end once the new roll is installed. The demanding nature of paper production means rolls require periodic inspection, maintenance, and often, refurbishment. Leading paper mill rolls manufacturers understand this and offer a suite of comprehensive after-sales services. This includes services like roll inspection, where experts assess the condition of rolls for wear, damage, or signs of impending failure using sophisticated diagnostic tools. More importantly, services like roll grinding are essential for maintaining the precise dimensions, crown, and surface finish necessary for optimal performance. Over time, rolls can wear unevenly, affecting nip pressure distribution and leading to issues like caliper variations or moisture profiles in the paper web. Precision grinding restores the roll’s geometry to its original specifications or adjusts it based on current operational needs. Refurbishment services can extend the life of significantly worn or damaged rolls, potentially including cover removal, core repair, resurfacing, and re-covering. Engaging in planned maintenance and refurbishment programs, including regular roll grinding services for paper mills, is often far more cost-effective than waiting for a roll failure and requiring an emergency replacement. It ensures continuous peak performance and prevents unexpected downtime. Partnering with a manufacturer who can provide reliable, high-precision maintenance and refurbishment services is crucial for maximizing the return on your roll investment and maintaining consistent production quality.
Refurbishment and Extending Roll Lifespan
In the continuous operation of a paper mill, rolls are subject to wear, fatigue, and damage. Replacing large, specialized rolls can be a significant capital expense. This is why the ability to effectively refurbish and extend the lifespan of existing rolls is a vital service offered by premier paper roll manufacturers. Refurbishment goes beyond simple grinding; it can involve stripping off old covers or coatings, inspecting and repairing the roll core for any structural issues, rebuilding worn journals or bearing surfaces, and then applying new covers or coatings before precision grinding and balancing. Services like calender roll refurbishment, for instance, are critical because calender rolls require extremely high precision and surface finish to impart the desired properties to the paper. A skilled manufacturer can assess whether a roll is a candidate for refurbishment, perform the necessary work to return it to like-new condition (or better, with updated materials), and save the mill considerable cost compared to purchasing a new roll. This service requires specialized equipment, expertise in various repair techniques (welding, machining), and the ability to apply new covers or coatings correctly. A manufacturer who excels in refurbishment acts as a true partner, helping mills manage their assets efficiently and sustainably. It’s a testament to their commitment to supporting their customers throughout the entire lifecycle of the paper machine roll, ensuring value far beyond the initial purchase.
Partnering for Success: Beyond the Transaction
Choosing paper mill rolls manufacturers is not just about procurement; it’s about forging a partnership. A reliable manufacturer acts as an extension of your maintenance and engineering teams, providing technical support, troubleshooting assistance, and expert advice. They should be proactive in helping you optimize roll performance, perhaps suggesting alternative materials or coatings that could improve efficiency or lifespan based on their experience with similar applications. This level of partnership is built on trust, reliability, and clear communication. It means the manufacturer understands your production schedule and can deliver new or refurbished rolls on time to minimize downtime. It means they stand behind their products and services, addressing any issues promptly and effectively. Furthermore, a good partner will invest in understanding your unique challenges and goals, using that insight to inform their recommendations and service offerings. They might offer training for your maintenance staff on roll handling and care, or provide detailed performance reports on refurbished rolls. This level of engagement goes far beyond a simple transactional relationship. It’s about having a trusted resource you can rely on for critical components and services that directly impact your mill’s bottom line. When evaluating potential suppliers, consider not just their manufacturing capabilities but also their track record for service, responsiveness, and collaborative problem-solving. Who do you want standing by your side when a critical roll needs immediate attention?
Innovation and the Future of Paper Roll Technology
The paper industry is constantly evolving, driven by demands for higher quality, increased speed, improved efficiency, and reduced environmental impact. Leading paper mill rolls manufacturers are at the forefront of innovation, developing new materials, surface technologies, and manufacturing processes to meet these challenges. This includes research into lighter, stronger composite materials, developing coatings that enhance release and reduce sticking for faster speeds, or creating intelligent rolls equipped with sensors to monitor performance characteristics like temperature and pressure in real-time. Automation and digitalization are also playing a growing role in roll manufacturing and maintenance, enabling even higher precision and more consistent quality. Manufacturers are exploring advanced analytics to predict roll wear and optimize maintenance schedules, moving towards a more proactive and predictive approach. Investing in R&D is crucial for a manufacturer to remain competitive and continue offering cutting-edge solutions. When selecting a partner, consider their commitment to innovation and their vision for the future of roll technology. Are they just maintaining the status quo, or are they actively developing the next generation of rolls that can help your mill achieve new levels of performance? This forward-thinking perspective is a strong indicator of a manufacturer’s long-term reliability and value.
Selecting Your Ideal Manufacturing Partner
In conclusion, the choice of paper mill rolls manufacturers is a critical decision with long-term implications for your mill’s productivity, product quality, and profitability. Look for manufacturers who demonstrate exceptional engineering expertise, utilize advanced manufacturing processes, maintain rigorous quality control, and offer comprehensive custom engineering and after-sales services, including vital refurbishment capabilities. Prioritize partners who invest in innovation and are willing to work collaboratively to understand and address your specific operational needs. Their ability to provide high-quality, durable rolls optimized for your machine, coupled with reliable maintenance and support, is key to minimizing downtime and maximizing operational efficiency. Choosing the right manufacturer is an investment in peace of mind and a strategic move towards achieving peak performance in your paper production. We understand the complexities and pressures you face. Our commitment is to provide rolls and services that not only meet but exceed the demanding requirements of modern paper mills, ensuring precision, durability, and performance you can count on, roll after roll. Ready to explore how a dedicated partner can enhance your mill’s operation?
For more detailed information, please visit our official website: paper mill rolls manufacturers