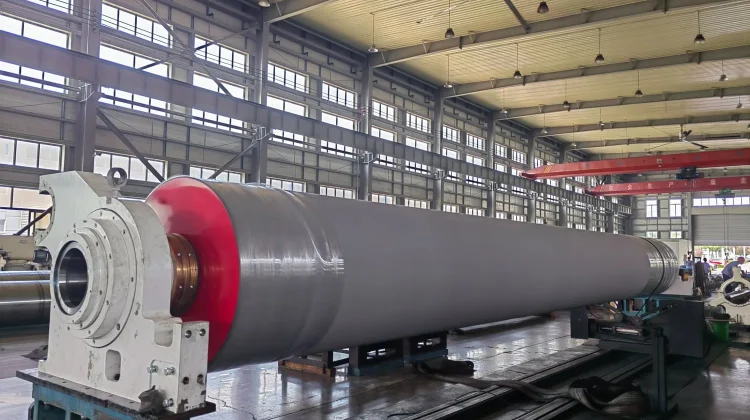
Choosing Top Paper Machine Rolls Manufacturers
In the demanding world of pulp and paper production, the reliability and performance of machinery are absolutely critical. At the heart of these complex systems are the paper machine rolls. These aren’t just simple cylinders; they are precision-engineered components that dictate everything from paper sheet formation and dewatering efficiency to surface finish and overall machine speed. Frankly speaking, the quality of these rolls directly impacts the quality and cost-effectiveness of the final paper product. Therefore, partnering with experienced and reputable Paper machine rolls manufacturers is not merely a procurement decision; it’s a strategic investment in the operational stability and profitability of a paper mill. Have you ever stopped to consider just how much stress and wear these rolls endure on a daily basis, operating in harsh, wet, and high-temperature environments? Their ability to withstand these conditions while maintaining precise dimensions and surface properties is a testament to advanced engineering and manufacturing expertise.
The Core Function: Why Rolls Matter in Paper Production
The paper machine itself is a marvel of industrial engineering, a long sequence of sections where a watery slurry of fibers is transformed into a finished paper web. Each section relies heavily on its set of specialized rolls to perform specific tasks. In the forming section, rolls help distribute the fiber suspension evenly onto the moving wire. The press section uses massive rolls under immense pressure to squeeze water out of the nascent sheet, dramatically increasing its dryness and strength. Dryer section rolls, often heated, support the sheet as the remaining moisture is evaporated. Finally, calender and reel rolls refine the surface finish and wind the completed paper. The subtle interactions between the sheet and the roll surfaces, the precise nip pressures, and the controlled speeds are all orchestrated by these cylindrical workhorses. Any imperfection – be it surface wear, imbalance, or dimensional deviation – can lead to sheet breaks, quality defects, reduced speed, and costly downtime. This highlights why selecting capable Paper machine rolls manufacturers who understand these intricate processes is paramount for seamless mill operations.
Navigating the Landscape of Paper Machine Roll Types
The variety of rolls within a single paper machine is extensive, each designed for a specific role and location. You have forming rolls like breast rolls and couch rolls, press rolls including plain press rolls, grooved rolls, blind-drilled rolls, and suction press rolls, each with unique surface patterns or internal designs to handle water removal. Dryer section rolls are typically large diameter steel or cast iron cylinders designed to withstand high temperatures. Calender stacks employ hard nip rolls (often chilled cast iron) and softer rolls to achieve the desired smoothness and caliper. Reel spools handle the final winding of the paper jumbo roll. Beyond these primary functional rolls, there are numerous guide rolls, felt rolls, and wire rolls that ensure proper tension and path for the felts and wires that carry the sheet. Understanding the specific requirements for each roll type – in terms of material, surface hardness, coating, and internal construction – is crucial for paper mills, and a skilled manufacturer can guide this selection process effectively. It’s worth noting that the demands on these different roll types vary significantly, requiring manufacturers to possess diverse expertise.
Engineering Excellence: The Manufacturing Process Defined
Producing high-quality paper machine rolls is a complex undertaking that demands precision engineering and rigorous quality control at every stage. It begins with the selection of appropriate base materials, which can range from various grades of steel and cast iron to composites, depending on the roll’s application. The core is then typically fabricated, often involving intricate welding for hollow rolls or precise casting. Machining follows, where the cylindrical shape is achieved with tolerances measured in microns. Balancing is a critical step; rolls operating at high speeds must be perfectly balanced to prevent vibration, which can damage the machine and compromise paper quality. Surface finishing is another key area, involving grinding, polishing, and potentially specialized coatings or coverings (like rubber, composite, or ceramic) tailored to the roll’s function and the type of paper being produced. Reputable Paper machine rolls manufacturers invest heavily in advanced machining equipment, non-destructive testing, and skilled technicians to ensure each roll meets the exacting standards required for reliable performance in the harsh mill environment. Frankly speaking, achieving the necessary precision and durability requires a deep understanding of both metallurgy and mechanics.
Choosing Your Partner: What to Look for in Manufacturers
When searching for Paper machine rolls manufacturers, simply finding a list is not enough. You need to evaluate potential partners based on several key criteria to ensure they can meet your mill’s specific needs. Experience in the industry is paramount; a manufacturer with a long history likely understands the nuances and challenges of paper production and roll performance. Technological capability is also vital – do they have modern machining, balancing, and testing equipment? What about their expertise in applying advanced coatings and coverings? Quality control processes should be robust, ideally with certifications like ISO 9001. Consider their capacity for customization; can they design and build rolls to your exact specifications or modify existing ones? After-sales support is equally important, including installation assistance, troubleshooting, and maintenance services. Finally, assess their reputation within the industry – what do their existing customers say about their reliability and responsiveness? Choosing the right manufacturer is a long-term decision that impacts operational efficiency and cost.
Innovation in Materials and Coatings for Enhanced Performance
The performance of paper machine rolls is significantly enhanced by advancements in materials science and surface technology. Manufacturers are continuously developing new coatings and coverings to improve roll longevity, wear resistance, chemical resistance, and even properties like release (preventing paper sticking). For instance, ceramic coatings offer exceptional hardness and abrasion resistance, ideal for challenging positions. Composite roll coverings can provide a combination of resilience, chemical resistance, and lighter weight compared to traditional rubber. Understanding the specific demands of your machine sections and the types of paper you produce will help determine which materials and coatings are most suitable. A forward-thinking manufacturer will be knowledgeable about these innovations and able to recommend solutions that can lead to increased run times, reduced maintenance, and improved paper quality. Interestingly enough, the right coating can sometimes completely transform a roll’s performance characteristics, extending its service life dramatically and contributing to overall energy savings.
Beyond Manufacturing: Essential Maintenance and Service Offerings
The lifecycle of a paper machine roll doesn’t end when it’s installed. Regular maintenance, inspection, and timely service are critical to maximizing its operational life and preventing unexpected failures. Reputable Paper machine rolls manufacturers often provide comprehensive service programs. This includes routine inspection services to detect early signs of wear or damage, in-situ or workshop grinding and polishing to restore the roll’s surface profile and finish, dynamic balancing to correct imbalances that develop over time, and repair services for damage like journal wear or shell cracks. Having a manufacturer who can provide these essential paper roll maintenance services simplifies the process and ensures that the work is done by experts who understand the roll’s original specifications. Relying on a manufacturer with strong service capabilities can minimize downtime associated with roll issues and help maintain peak machine performance.
Tailored Solutions: The Value of Custom Paper Machine Rolls
While standard roll designs exist, many paper machines, especially older ones or those producing specialty grades, require customized solutions. This is where the expertise of Paper machine rolls manufacturers truly shines. They can work closely with mill engineers to design and produce rolls with specific dimensions, materials, surface geometries (like special grooving patterns), or internal features (like steam heating or water cooling) to meet unique process requirements. Whether it’s a roll needed for a non-standard machine width, a specialized nip requirement, or a need to combat a particular sheet defect like barring or streaking, a manufacturer capable of creating custom paper machine rolls is an invaluable asset. This ability to provide tailored solutions ensures optimal integration into the existing machine and addresses specific operational challenges effectively. Many experts agree that customization often leads to significant improvements in efficiency and product quality that standard off-the-shelf rolls simply cannot achieve.
Upholding Standards: Quality Control in Roll Production
For components as critical as paper machine rolls, rigorous quality control is non-negotiable. Leading manufacturers implement comprehensive quality assurance programs throughout their production process. This begins with verifying the quality of raw materials. During manufacturing, dimensional checks are constant, ensuring precise diameters, lengths, and concentricity. Surface finish is meticulously measured, often using sophisticated profilometers. Non-destructive testing methods like ultrasonic testing, magnetic particle testing, and eddy current testing are employed to detect any internal flaws or cracks that could compromise the roll’s integrity. Dynamic balancing is performed on high-speed balancing machines to minimize vibration during operation. Documentation is also key, providing mills with detailed reports on material properties, dimensions, balance certificates, and surface profiles. Choosing manufacturers who prioritize these stringent quality control measures provides confidence in the reliability and performance of the rolls supplied, ultimately protecting the mill’s investment and minimizing operational risks.
Looking Ahead: Future Trends in Roll Manufacturing
The paper industry is constantly evolving, and so too is the manufacturing of paper machine rolls. We are seeing increased interest in sustainable manufacturing practices, including using more recyclable materials and reducing energy consumption in the production process. There is also a growing trend towards integrating smart technology into rolls, such as embedded sensors that can monitor temperature, vibration, and nip pressure in real-time, providing valuable data for predictive maintenance and process optimization. Lightweight materials are also being explored to improve energy efficiency and facilitate easier handling. Manufacturers are also focusing on developing coatings and coverings that are more environmentally friendly and easier to maintain. Staying abreast of these trends is important for mills looking to invest in rolls that will not only perform reliably today but also contribute to the future efficiency and sustainability of their operations. The best manufacturers are those who are actively engaged in researching and implementing these future technologies.
Selecting Wisely: A Strategic Decision for Mill Success
In conclusion, paper machine rolls are foundational elements in the pulp and paper industry, directly influencing the quality, speed, and efficiency of production. Their selection and maintenance are critical factors in a mill’s success. Choosing the right Paper machine rolls manufacturers involves careful consideration of their experience, technological capabilities, quality control, range of services (including crucial paper roll maintenance services), and ability to provide customized solutions. A reliable manufacturer acts as a strategic partner, offering expertise and support throughout the roll’s lifecycle, from initial design and production of potentially custom paper machine rolls to ongoing maintenance and repair. Investing in high-quality rolls from a reputable source minimizes the risk of costly downtime, improves product consistency, and enhances overall operational profitability. Take the time to thoroughly evaluate your options and partner with a manufacturer who demonstrates a deep understanding of your specific needs and challenges. What steps will you take today to ensure your paper machine rolls are contributing optimally to your mill’s performance?
For more detailed information, please visit our official website: Paper machine rolls manufacturers