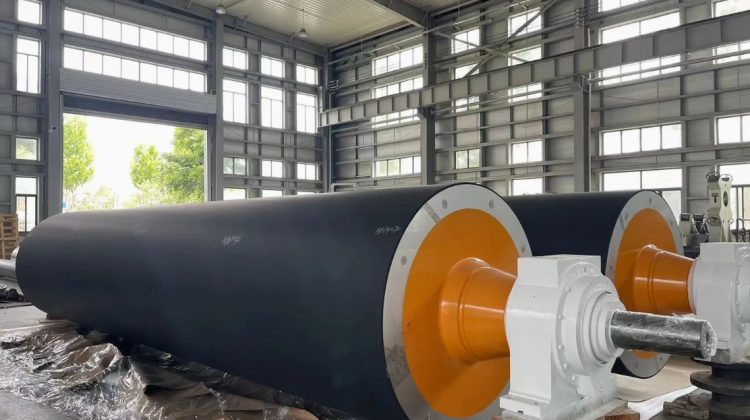
In the intricate and demanding world of papermaking, numerous components work in concert to transform raw pulp into the vast array of paper products we rely on daily. Among these, paper machine rollers stand out as critical, albeit often unsung, heroes. These robust cylinders are fundamental to nearly every stage of the paper manufacturing process, from initial sheet formation and dewatering to pressing, drying, and finishing. While they may seem like straightforward components, the quality, design, and precision of your paper machine rollers can profoundly impact your operational efficiency, final product quality, and ultimately, your bottom line.
1. The Direct Impact on Paper Quality
The first and most apparent reason to invest in high-quality paper machine rollers is their direct influence on the attributes of the paper produced. Whether it’s a press roll ensuring uniform moisture removal and sheet consolidation, a calender roll imparting desired smoothness and gloss, or a guide roll maintaining web stability, each roller plays a specific role in shaping the final product.
Inferior or poorly maintained rollers can lead to a host of paper defects, including:
- Uneven Profiles: Inconsistent roller surfaces or improper crowning can result in variations in paper thickness and density.
- Surface Imperfections: Damaged or worn roller covers can transfer marks, barring, or streaks onto the paper sheet.
- Reduced Strength: Inefficient pressing due to roller issues can leave excessive moisture, compromising the paper’s final strength characteristics.
- Sheet Breaks: Poor web handling and tension control, often linked to guide roll performance, can lead to costly sheet breaks and production halts.
Conversely, high-quality, precision-engineered rollers ensure consistent pressure, smooth surfaces, and reliable web transport, contributing directly to superior paper quality that meets customer expectations and industry standards.
2. Enhancing Operational Efficiency and Reducing Downtime
Beyond product quality, the caliber of your paper machine rollers significantly affects your mill’s overall operational efficiency. Rollers are subjected to immense mechanical stresses, high temperatures, and often corrosive environments. High-quality rollers are designed and manufactured with superior materials and robust construction to withstand these demanding conditions.
This translates to:
- Longer Service Life: Durable rollers require less frequent replacement, minimizing unscheduled downtime and associated maintenance costs.
- Improved Runnability: Precision-balanced and accurately aligned rollers contribute to smoother machine operation and higher sustainable speeds.
- Reduced Maintenance: Rollers with advanced cover materials and sealing technologies often require less frequent regrinding and specialized maintenance.
- Energy Savings: Efficient dewatering in the press section, facilitated by well-designed press rolls, can reduce the steam load in the dryer section, leading to significant energy cost reductions.
Investing in quality rollers means investing in uptime, productivity, and a more streamlined, cost-effective operation.
3. The Value of Precision Engineering and Customization
Not all paper machines or applications are the same. The optimal roller solution often requires careful consideration of specific operational parameters, paper grades being produced, and desired end-product characteristics. This is where the expertise of a specialized paper machine roller manufacturer becomes invaluable.
High-quality rollers are a product of:
- Advanced Material Science: Selecting the right core materials, alloys, and cover compounds (rubber, polyurethane, composite, stone, etc.) for specific applications and resistance to wear, heat, and chemicals.
- Precision Manufacturing: Utilizing advanced CNC machining, grinding, and balancing techniques to achieve exacting dimensional tolerances and surface finishes.
- Custom Design Capabilities: The ability to engineer rollers with specific crowning, grooving patterns, drilling (for suction or blind drilled rolls), and other features tailored to optimize performance for a particular machine position or paper grade.
Partnering with a manufacturer who understands these intricacies ensures you receive rollers that are not just components, but engineered solutions designed to enhance your specific papermaking process.
Conclusion: A Vital Investment for a Competitive Edge
In conclusion, paper machine rollers are far more than just rotating cylinders; they are pivotal investments that directly influence the quality of your paper, the efficiency of your operations, and the profitability of your mill. By prioritizing high-quality, precision-engineered rollers from a reputable and experienced manufacturer, you are laying a crucial foundation for producing superior products, minimizing operational disruptions, and maintaining a competitive edge in the dynamic paper industry. The unsung heroes of your paper machine deserve the best, as their performance is intrinsically linked to your success.
Hi, this is a comment.
To get started with moderating, editing, and deleting comments, please visit the Comments screen in the dashboard.
Commenter avatars come from Gravatar.