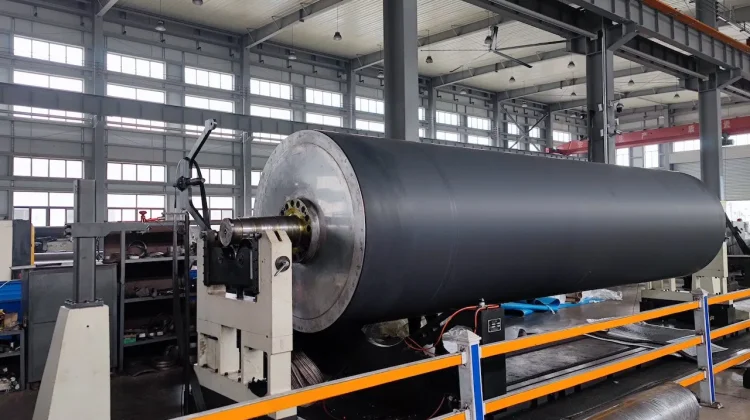
Choosing a Leading Paper Mill Rolls Manufacturer
In the complex world of paper production, every component plays a critical role in ensuring efficiency, quality, and ultimately, profitability. Among these, the various rolls used throughout the paper machine are undeniably central to the process. From forming and pressing to drying and calendering, these rolls are subjected to immense pressures, high temperatures, and demanding operating environments. Their performance dictates everything from paper thickness and moisture content to surface finish and web tension. Frankly speaking, the operational heart of a paper mill beats in time with the rhythm of its rolls. This is precisely why selecting the right paper mill rolls manufacturer isn’t just a purchasing decision; it’s a strategic partnership that directly impacts your mill’s output and bottom line. A manufacturer doesn’t just supply parts; they provide engineered solutions designed to withstand the rigors of continuous operation, enhance machine speed, reduce downtime, and improve paper quality. Have you ever stopped to consider the sheer engineering precision required to produce a roll that might be several meters long, weigh tonnes, and yet maintain micron-level tolerances across its surface? It’s a remarkable feat of industrial manufacturing, and identifying a manufacturer with this level of expertise is paramount for any mill looking to optimize its operations.
Understanding Paper Machine Rolls: Types and Function
The paper machine is a marvel of sequential processes, and each stage relies on specific types of rolls engineered for unique tasks. In the forming section, rolls like couch rolls and forming rolls help dewater the pulp slurry and form the nascent paper web. Moving into the press section, press rolls, often covered with specialized materials, squeeze out more water under tremendous pressure, compacting the web and increasing its strength. The drying section utilizes large-diameter drying cylinders heated internally, alongside guide rolls and felt rolls, to evaporate remaining moisture. Finally, the calender section uses calender rolls, typically made of chilled cast iron or covered with softer materials, to smooth and finish the paper surface, controlling caliper and gloss. Interestingly enough, the specific design, material, and surface characteristics of each roll type are critical for its function and the quality of the final paper product. A slight imperfection, imbalance, or inappropriate coating can lead to web breaks, uneven dewatering, poor finish, and increased wear on other components. Therefore, understanding the distinct requirements of each roll position and partnering with a manufacturer who possesses deep knowledge across this entire spectrum is non-negotiable for maintaining high performance standards.
The Expertise of a Leading Paper Mill Rolls Manufacturer
What truly distinguishes a leading paper mill rolls manufacturer goes far beyond simply fabricating a cylindrical shape. It lies in their comprehensive expertise that spans design, material science, precision machining, and deep understanding of the paper production process itself. Such manufacturers don’t just work from blueprints; they collaborate with mills to understand their specific machine configurations, paper grades, operating speeds, and environmental factors. They offer consulting on optimal roll designs, material selection – whether it’s specialized alloys for strength or specific composite materials for reduced weight or enhanced performance – and appropriate surface coatings or coverings tailored to the roll’s function (e.g., rubber for press rolls, ceramic for wear resistance, chrome for hardness). Their engineering teams use advanced modeling and simulation software to predict roll behavior under load and thermal stress. Furthermore, they have the capability to produce not just standard rolls but also highly specialized paper machine rolls designed for unique applications or demanding conditions. This holistic approach, combining theoretical knowledge with practical manufacturing capability, ensures that the rolls supplied are not just components, but optimized solutions contributing directly to the mill’s operational success.
Precision Manufacturing and Quality Assurance
The manufacturing process itself is a testament to precision engineering when it comes to paper mill rolls. Producing a roll that is perfectly straight, balanced, and dimensionally accurate along its entire length, sometimes exceeding 10 meters, is an immense technical challenge. Leading manufacturers employ state-of-the-art machining equipment, including large-capacity lathes and grinders, capable of achieving micron-level tolerances. Balancing is another critical step; dynamic balancing ensures the roll runs smoothly at high speeds, preventing vibration that can degrade paper quality and damage the machine. Surface finish is equally vital, with techniques like grinding, polishing, and superfinishing applied to achieve the exact roughness required for each roll position. Coatings and coverings are applied with meticulous control to ensure uniform thickness and adhesion. To be honest, without rigorous quality control at every stage – from material inspection and machining verification to balancing tests and final dimension checks – even the best design is useless. Manufacturers invest heavily in sophisticated testing equipment and adhere to stringent quality management systems to guarantee that every roll leaving their facility meets the demanding specifications required for optimal performance in a high-speed paper machine environment. This commitment to quality is what minimizes the risk of premature failure and unexpected downtime in the mill.
Lifecycle Services: Maintenance, Repair, and Refurbishment
A paper mill roll’s journey doesn’t end when it’s installed in the machine. These components are subject to continuous wear and tear, making regular maintenance and timely repair services essential for maximizing their lifespan and performance. A comprehensive paper mill rolls manufacturer offers a suite of lifecycle services, including routine inspections, grinding and profiling to restore the correct shape and surface finish, balancing to correct imbalances that develop over time, and re-coating or re-covering worn surfaces. When damage occurs, such as bearing journal wear or shell damage, repair services can often restore the roll to operational condition, providing a cost-effective alternative to replacement. Refurbishment services can extend the life of older rolls, potentially incorporating updated materials or coatings to improve performance beyond original specifications. Partnering with a manufacturer who can provide these services ensures that your rolls are maintained to the highest standards, preventing unexpected failures and prolonging the asset’s usable life. Neglecting roll maintenance inevitably leads to decreased efficiency, poor paper quality, and eventually, costly emergency repairs or replacements. Proactive service is key to stable mill operations.
Innovation and Custom Solutions
The paper industry is constantly evolving, with mills striving for higher speeds, increased efficiency, and the production of new paper grades with specific properties. A forward-thinking paper mill rolls manufacturer doesn’t just meet existing needs; they anticipate future challenges and develop innovative solutions. This includes research and development into new materials offering improved wear resistance, higher strength-to-weight ratios, or better thermal conductivity. They explore advanced coating technologies, such as carbides or ceramics, which provide exceptional durability and specific surface characteristics. Furthermore, they excel in creating custom paper machine rolls designed to meet the unique requirements of a particular machine or process. This might involve engineering rolls with specialized internal cooling or heating systems, developing unique crown profiles to compensate for deflection under load, or designing lightweight composite rolls for faster acceleration and reduced energy consumption. Partnering with a manufacturer committed to innovation ensures you have access to the latest advancements in roll technology, helping your mill stay competitive and achieve its production goals, whether you need standard components or highly specialized paper machine rolls for a niche application.
Choosing the Right Partner: What to Look For
Given the critical nature of paper mill rolls, selecting the right manufacturing partner requires careful consideration. What criteria should guide your decision? First and foremost, look for a manufacturer with a proven track record and extensive experience in the paper industry. Their understanding of the unique challenges and requirements of paper machines is invaluable. Assess their engineering and manufacturing capabilities: Do they have the necessary equipment for high-precision machining, balancing, and coating? What are their quality control processes like? Ask about their material science expertise and their ability to recommend the best materials and coatings for your specific applications. Don’t overlook their service capabilities; a manufacturer offering comprehensive lifecycle support, including inspection, maintenance, and repair, can be a significant asset. Consider their responsiveness and customer support – can they provide timely technical assistance and address urgent needs? Many experts agree that a collaborative approach, where the manufacturer acts as a true partner, understanding your operational goals and challenges, is key to long-term success. Choosing a manufacturer solely based on price can be a costly mistake in the long run if it compromises quality and reliability.
The Bottom Line: Impact on Production and Profitability
The choice of your paper mill rolls manufacturer has a direct and significant impact on your mill’s operational efficiency and overall profitability. High-quality, precisely manufactured rolls reduce the risk of web breaks, minimizing costly downtime and lost production. Their correct crown profile and surface finish ensure consistent dewatering and uniform paper properties, leading to a higher quality final product and reduced waste. Properly balanced rolls contribute to smoother machine operation, extending the life of bearings and other machine components. Furthermore, rolls with durable coatings and appropriate materials require less frequent maintenance and replacement, reducing operational costs. Investing in rolls from a reputable industrial roll manufacturing expert is an investment in the reliability, speed, and quality of your entire paper machine. It prevents unforeseen issues, improves the consistency of your output, and ultimately enhances your mill’s competitive position in the market. It’s worth noting that while the initial cost might seem higher for premium rolls and services, the total cost of ownership, factoring in reduced downtime, lower maintenance expenses, and improved product quality, is often significantly lower.
In conclusion, the performance of your paper machine is intrinsically linked to the quality and reliability of its rolls. Partnering with an experienced, technologically advanced, and service-oriented paper mill rolls manufacturer is not a luxury, but a necessity for any mill aiming for peak performance. Such a partner provides not just components, but engineered solutions, expert guidance, and ongoing support that help you optimize production, reduce costs, and improve paper quality. Make sure to evaluate potential manufacturers based on their expertise, capabilities, quality standards, and commitment to service. Choosing wisely today will pay dividends in operational stability and profitability for years to come. Taking the next step to consult with leading experts can provide valuable insights tailored to your specific mill requirements.
For more detailed information, please visit our official website: paper mill rolls manufacturer