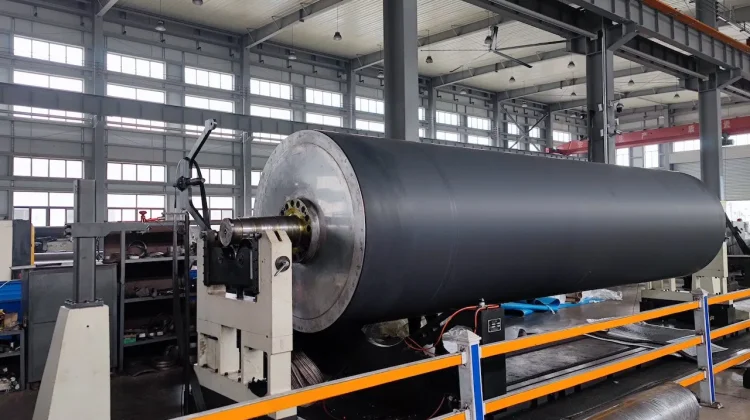
Stone Roller for Toilet Paper & Paper Mill Machinery (Spare Part)
Understanding the Role of Stone Rollers in Paper Production
Stone rollers are the unsung heroes of paper manufacturing, particularly in toilet paper production. These precision-engineered components serve as critical spare parts in paper mill machinery, ensuring smooth operation and consistent product quality. The unique surface characteristics of stone rollers make them indispensable for achieving the right texture and absorbency in toilet paper. Unlike conventional metal rollers, stone rollers provide a gentler yet more effective processing surface that prevents fiber damage while maintaining optimal moisture levels during production.
Why Stone Rollers Outperform Traditional Alternatives
To be honest, many paper manufacturers don’t realize the significant advantages stone rollers offer over traditional metal or rubber alternatives. The porous nature of stone allows for better moisture control during the pressing stage, which is crucial for producing soft yet strong toilet paper. Interestingly enough, stone rollers also maintain their surface integrity longer than synthetic alternatives, reducing downtime for maintenance. This durability translates directly to cost savings in paper mill operations, making them a smart investment as spare parts.
Key Applications in Toilet Paper Manufacturing
In toilet paper production, stone rollers play multiple critical roles. They’re primarily used in the pressing section where the paper web is formed and dried. The stone surface creates micro-pores in the paper that enhance absorbency – a key quality factor for toilet paper. Additionally, these rollers help maintain consistent caliper (thickness) across the entire sheet, preventing the common issue of uneven rolls that can jam packaging equipment downstream.
Technical Specifications That Matter
When selecting stone rollers as spare parts for paper mill machinery, several technical specifications require attention. The stone’s hardness rating (typically between 6-8 on the Mohs scale) determines its durability and resistance to wear. Grain size affects the paper’s surface finish, with finer grains producing smoother paper. The roller’s diameter and length must precisely match the machine’s specifications to ensure proper tension and alignment during operation. Many experts agree that custom-engineered stone rollers often outperform standard options in specialized applications.
Maintenance and Longevity Considerations
Proper maintenance extends the service life of stone rollers significantly. Regular cleaning with specialized solutions prevents fiber buildup that can degrade performance. It’s worth noting that stone rollers should be inspected periodically for micro-cracks or surface wear. Unlike metal components, stone rollers can often be refinished rather than replaced, offering substantial cost savings. The key is implementing a preventive maintenance schedule that includes vibration analysis and surface profiling.
Common Issues and Troubleshooting
Have you ever wondered why some paper mills experience inconsistent product quality despite using high-end equipment? Often, the culprit is worn or improperly maintained stone rollers. Common issues include uneven wear patterns that create streaks in the paper, or excessive vibration that affects roll formation. Frankly speaking, most of these problems can be prevented with proper installation and regular maintenance checks. When issues do arise, they’re typically resolved through precision balancing or surface reconditioning rather than complete replacement.
Selecting the Right Stone Roller for Your Operation
Choosing the optimal stone roller involves evaluating several factors. Production volume requirements dictate the necessary roller diameter and width. The type of pulp being processed affects the ideal stone composition – softer stones work better with recycled fibers while harder stones handle virgin pulp more effectively. Machine speed capabilities must also be considered, as higher speeds require more precisely balanced rollers to prevent vibration issues. In my experience, consulting with specialists who understand both the machinery and the paper production process yields the best results.
Innovations in Stone Roller Technology
Recent advancements in stone roller technology have brought significant improvements to paper manufacturing. Composite stone materials now offer enhanced durability while maintaining the traditional benefits of natural stone. Some manufacturers have developed hybrid rollers that combine stone surfaces with reinforced cores for better structural integrity. These innovations allow for higher operating speeds and longer intervals between maintenance cycles, directly impacting production efficiency and cost-effectiveness.
Cost-Benefit Analysis of Stone Rollers
While stone rollers may have a higher initial cost compared to some alternatives, their long-term value becomes apparent through several factors. The extended service life reduces replacement frequency. Improved product quality leads to fewer rejects and customer complaints. Energy savings result from more efficient moisture removal during pressing. When considering the total cost of ownership, stone rollers often prove to be the most economical choice for serious paper manufacturers. The key is selecting the right specification for your particular production requirements.
Integrating Stone Rollers into Existing Systems
Upgrading to stone rollers in existing paper mill machinery requires careful planning. Compatibility with current drive systems must be verified. The machine’s frame and bearings may need reinforcement to handle the different weight characteristics of stone rollers. Production schedules should account for the adjustment period as operators become accustomed to the different handling characteristics. Many successful implementations follow a phased approach, replacing rollers one section at a time to minimize production disruption.
For more detailed information, please visit our official website: Stone Roller for Toilet Paper & Paper Mill Machinery (Spare Part)