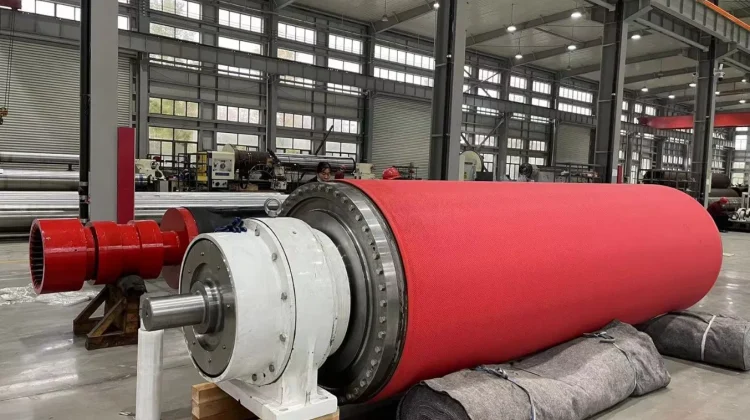
Finding Top Paper Mill Rollers Manufacturers
Paper production is an intricate process, a high-speed ballet of pulp, water, and machinery. At the heart of this complex dance are the rollers, unsung heroes that guide, press, dry, and finish the paper web. These cylindrical components are subjected to immense forces, high temperatures, and challenging chemical environments, making their design, manufacture, and maintenance absolutely critical to the efficiency and quality of the entire operation. Frankly speaking, without reliable, high-performance rollers, a paper mill simply cannot function at its peak, or perhaps not function at all. This is why the choice of your paper mill rollers manufacturers is one of the most significant decisions you’ll make for your mill’s long-term success. It’s not just about buying a piece of equipment; it’s about partnering with an expert who understands the unique demands placed upon these vital components and possesses the capability to meet those demands consistently, year after year. The role of the roller goes far beyond simple conveyance; it’s integral to the physics and chemistry transforming a liquid slurry into a finished paper product. Have you ever truly considered the engineering marvel packed into every single roller within your machine?
Understanding the Critical Role of Paper Machine Rollers
To appreciate the importance of selecting expert paper mill rollers manufacturers, we first need to delve deeper into what these rollers actually do. Think about the journey of the paper web from the wet end to the reel. Rollers are involved at every stage. In the forming section, couch and guide rolls handle the fragile, wet web. In the press section, massive press rolls squeeze out water under thousands of pounds per linear inch of pressure – a process requiring incredible structural integrity and precise surface properties to avoid crushing the web or causing uneven moisture profiles. Dryer section rolls transport the sheet through scorching temperatures, demanding materials and coatings that can withstand heat and prevent sticking. Calendar rolls then iron the paper surface to achieve the desired smoothness and caliper, a step requiring extreme precision and hardness. Each application presents a unique set of challenges related to load, speed, temperature, chemical exposure, and required surface finish. A seemingly minor imperfection on a roller surface can lead to significant issues, from sheet breaks and poor quality to catastrophic equipment failure. This isn’t merely about keeping the paper moving; it’s about actively participating in the dewatering, consolidation, and finishing processes that define the final product’s characteristics. The engineering behind each roller, tailored to its specific position and function, is paramount.
The Harsh Environment and Its Impact on Rollers
Operating within a paper mill’s aggressive environment takes a severe toll on machinery, and rollers are particularly vulnerable. They are exposed to high temperatures, often exceeding 120°C in dryer sections. The presence of water, chemicals used in pulp processing (acids, alkalis, sizing agents), and sometimes abrasive fillers can lead to corrosion and wear on metal surfaces and degradation of coatings. Furthermore, the continuous mechanical stress from pressure, bending forces, and rotational speed contributes to fatigue and potential failure. Sheet breaks, which are an inevitable part of paper production, can cause severe damage to roller surfaces if not addressed immediately, leading to dents, scratches, or coating damage that propagates and necessitates repair or replacement. Interestingly enough, even seemingly minor issues like vibrations caused by imbalances can lead to premature bearing failure or affect paper quality. Managing these challenges requires rollers built with robust materials, expertly applied protective coatings, and precision engineering that accounts for thermal expansion and dynamic loading. Reliable paper mill rollers manufacturers understand these stresses intimately and design their products to not just withstand them, but to perform optimally despite them, ensuring longevity and consistent performance in unforgiving conditions. It’s a testament to their engineering prowess that these components can endure such a punishing lifecycle.
Key Qualities of Top Paper Mill Rollers Manufacturers
So, what exactly sets apart the leading paper mill rollers manufacturers from the rest? It boils down to a combination of deep industry knowledge, advanced manufacturing capabilities, and a commitment to quality. Firstly, expertise matters. Manufacturers with decades of experience in the paper industry understand the nuances of different paper grades, machine types, and operational philosophies. They can recommend the most suitable roller design, materials, and coatings for a specific application, rather than offering a generic solution. Secondly, manufacturing precision is non-negotiable. Producing rollers with the required dimensional accuracy, straightness, concentricity, and surface finish demands state-of-the-art machinery, skilled technicians, and stringent quality control processes. This includes everything from initial material inspection to final balancing and non-destructive testing. Poorly manufactured rollers can cause vibrations, uneven nip pressures, and premature wear, all of which negatively impact paper quality and machine efficiency. Thirdly, material science know-how is crucial. The choice of steel grade, the application of specialized coatings (like rubber, polymers, or ceramics), and surface treatments (like chrome plating or tungsten carbide) significantly affect a roller’s performance characteristics, durability, and resistance to wear and corrosion. A top manufacturer doesn’t just apply a coating; they select and apply the coating best suited to the specific operational demands of that roller’s position in the machine. It’s this combination of tailored knowledge and manufacturing excellence that differentiates the best suppliers.
Precision Engineering: The Foundation of Roller Performance
The manufacturing process for high-quality paper mill rollers is a masterclass in precision engineering. It starts with the selection of high-grade raw materials, typically specialized steels chosen for their strength, stiffness, and sometimes corrosion resistance. The machining process involves turning, grinding, and polishing to achieve tight tolerances on diameter, length, and geometry. For instance, achieving the exact crown profile on press rolls is critical for ensuring uniform pressure across the paper web width, which directly impacts dewatering efficiency and moisture profile uniformity. Balancing is another crucial step; high-speed rotation of a heavy roller requires dynamic balancing to minimize vibration, which can otherwise lead to bearing damage, structural fatigue, and sheet flutter. Surface finishing, whether through grinding, polishing, or coating application, determines the interaction between the roller and the paper web, influencing factors like grip, release, and surface properties imparted to the paper. For rolls requiring coatings, the application process itself is highly specialized, whether it’s rubber calendering, thermal spraying of ceramics or carbides, or polymer application. Each layer must be uniform, defect-free, and possess the intended hardness, elasticity, or wear resistance. Frankly speaking, the level of detail and control required at every stage, from casting the raw steel to the final micron-level surface finish, is astonishing and underscores why partnering with experienced paper mill rollers manufacturers is essential for mills prioritizing quality and uptime. They are, in essence, crafting high-precision instruments designed to perform reliably under extreme stress.
Types of Paper Mill Rollers and Their Specific Needs
Paper machines utilize a diverse array of rollers, each serving a distinct purpose and facing unique operational demands. Understanding these differences highlights why a one-size-fits-all approach is ineffective and why specialized knowledge from paper mill rollers manufacturers is so valuable. Couch rolls, often located at the wet end, help support and consolidate the fragile sheet immediately after the headbox. They often require vacuum capabilities to assist in initial dewatering. Press rolls, as mentioned, apply massive pressure to remove water mechanically; they need exceptional structural strength, precise crowning, and specialized covers (rubber, polymer, composite) designed for specific nip pressures and dewatering goals. Dryer cans (though technically cylinders, they function like rollers) are large, heated drums that evaporate remaining moisture; they must withstand high internal steam pressures and external heat, requiring robust construction and smooth, durable surfaces. Calendar rolls, used in the finishing section, apply high pressure and sometimes heat to densify and smooth the paper surface; these are often made of chilled cast iron or covered with polymer or composite materials, demanding extreme hardness, surface finish, and precision grinding. Guide rolls, while seemingly simple, are vital for controlling the paper web’s path and tension throughout the machine, requiring good balance, reliable bearings, and sometimes specialized surfaces to prevent build-up or slippage. Each type presents unique engineering challenges related to load bearing, thermal management, surface integrity, and dynamic performance. A competent manufacturer specializes in addressing these distinct requirements, ensuring each roller is optimized for its specific role.
Choosing the Right Partner: Selecting Paper Machine Roller Suppliers
Given the critical nature of these components, the process of selecting your paper machine roller suppliers should be thorough and strategic. It’s not just about finding someone who can fabricate a cylinder; it’s about finding a long-term partner who can contribute to your mill’s operational efficiency and product quality. What should you look for? Firstly, assess their engineering capability and experience specifically within the paper industry. Do they have a track record of success with machines similar to yours? Can they offer insights into optimizing roller performance based on your specific pulp furnish and paper grades? Secondly, evaluate their manufacturing facilities and quality control procedures. Can they handle the size and weight of your required rollers? What testing and inspection processes do they employ throughout manufacturing? Ask about their materials sourcing and coating application expertise. Thirdly, consider their service and support capabilities. Do they offer installation assistance, alignment services, or ongoing maintenance advice? Can they provide refurbishment or repair services for existing rollers? A manufacturer who can support the entire lifecycle of the roller, from design and production to maintenance and repair, offers significant value. Finally, think about customization. Do they have the flexibility to produce custom paper machine rollers tailored to unique machine configurations or specific performance requirements, rather than only offering standard sizes? This ability to provide bespoke solutions is often a hallmark of a top-tier supplier who truly understands customer needs.
Assessing Quality and Reliability in Paper Mill Rollers Manufacturers
When evaluating potential paper mill rollers manufacturers, quality and reliability should be at the forefront of your assessment. How can you measure this? Look for certifications (like ISO 9001) that indicate a commitment to consistent quality management systems, although this is just a starting point. Ask about their specific quality control checks for rollers: material composition analysis, dimensional inspections, ultrasonic testing for internal defects, dynamic balancing reports, and detailed surface finish measurements. Request case studies or references from other paper mills to understand their real-world performance and customer satisfaction levels. A reliable manufacturer stands behind their products, offering clear warranties and responsive support if issues arise. Don’t hesitate to inquire about their design process – how do they calculate stress loads, predict deflection, or model thermal behavior for different roller types? Their willingness and ability to provide detailed technical explanations and data speak volumes about their engineering depth. Furthermore, consider their approach to packaging and shipping; proper handling is essential to prevent damage during transit, especially for large, precision-ground rolls. Ultimately, a manufacturer’s commitment to reliability is reflected in their transparency, their investment in technology and skilled personnel, and their proactive approach to preventing issues rather than just fixing them after they occur. Partnering with someone who prioritizes these aspects gives you confidence in the critical components running your machine.
Innovation and Future Trends in Roller Manufacturing
The world of paper manufacturing is constantly evolving, with demands for higher speeds, improved efficiency, and enhanced paper quality. Top paper mill rollers manufacturers aren’t just passive suppliers; they are active innovators contributing to these advancements. This includes developing new materials and coatings that offer improved wear resistance, better release properties, or higher load-bearing capacity. For instance, advanced composite materials are increasingly being used for certain roller applications due to their lighter weight, stiffness, and corrosion resistance compared to traditional steel. There’s also a trend towards ‘smart’ rollers equipped with sensors to monitor internal temperature, vibration, or bearing condition in real-time, allowing for predictive maintenance and preventing unexpected failures. Surface technologies are also advancing, with manufacturers exploring laser texturing or other novel methods to create optimal surface structures for specific functions like dewatering or sheet handling. Staying abreast of these innovations and investing in research and development is characteristic of a forward-thinking manufacturer. When you partner with a company that is pushing the boundaries of roller technology, you gain access to solutions that can provide a competitive edge, improving your mill’s performance not just today, but for years to come. It’s worth noting that innovation in roller design and manufacturing directly contributes to achieving higher machine speeds and reducing energy consumption, aligning with modern industry goals for sustainability and efficiency.
The Value of Partnering with Experienced Suppliers of Industrial Paper Rollers
Bringing all these elements together – expertise, precision manufacturing, quality materials, comprehensive service, and a commitment to innovation – illustrates the significant value derived from partnering with experienced supplier of industrial paper rollers. They offer more than just a physical product; they provide a solution package that minimizes risk and maximizes performance. A skilled manufacturer acts as a technical resource, helping you troubleshoot issues, optimize roller specifications for changing production needs, and plan for future upgrades. They can also provide invaluable insights into proper roller handling, storage, and maintenance practices within your mill, further extending the life and performance of their products. In my experience, the initial cost of a high-quality, custom-engineered roller from a reputable manufacturer is often offset many times over by reduced downtime, lower maintenance costs, improved paper quality, and increased machine speed over its operational life. Trying to save money by opting for cheaper, lower-quality rollers or manufacturers lacking specialized paper industry knowledge almost invariably leads to higher costs down the line due to premature failure, frequent repairs, and lost production. Investing in quality rollers from proven paper mill rollers manufacturers is an investment in the reliability and profitability of your entire paper machine. It’s a strategic decision that pays dividends in operational stability and product excellence.
Seamless Integration and Support: Beyond Just Manufacturing
A truly excellent paper mill rollers manufacturer understands that their job doesn’t end when the roller leaves their factory floor. Seamless integration and ongoing support are crucial components of the partnership. This can include providing detailed specifications and installation guidelines, offering on-site technical assistance during installation or commissioning, and helping with initial alignment and calibration to ensure the roller performs as designed from day one. Furthermore, access to timely repair and refurbishment services is vital for minimizing downtime. When a roller needs regrinding, recovering, or bearing replacement, a responsive manufacturer with the necessary facilities and expertise can turn it around quickly and efficiently, getting your machine back up and running. Preventative maintenance advice, condition monitoring recommendations, and spare parts availability also contribute significantly to operational continuity. Many experts agree that the relationship with a manufacturer should be viewed as a long-term partnership focused on optimizing the performance and lifespan of the rollers throughout their service life. This level of comprehensive support distinguishes the leaders in the field and provides paper mills with the confidence and reliability they need to operate effectively in a demanding global market. It’s the holistic approach to product and service that truly adds value.
Your Partner in Paper Production Excellence
Navigating the complexities of paper machine operations requires reliable components backed by expert support. Choosing the right partner among the many paper mill rollers manufacturers is a critical step towards achieving operational excellence, consistent paper quality, and maximized uptime. A manufacturer with deep industry knowledge, state-of-the-art manufacturing capabilities, a commitment to precision and quality control, and comprehensive service offerings provides the foundation for success. They don’t just sell you a product; they provide engineered solutions tailored to your specific machine and production needs, contributing to the overall efficiency and profitability of your mill. From selecting the right materials and coatings to ensuring micron-level precision and offering ongoing support, a top-tier manufacturer is invested in your mill’s performance. By focusing on quality, reliability, and partnership, you can secure rollers that withstand the harsh demands of the paper-making process and contribute positively to your bottom line. Don’t underestimate the impact that high-quality rollers from a reputable manufacturer can have on your production line. Are you confident that your current roller supplier is providing the level of quality and support necessary for peak performance?
For more detailed information, please visit our official website: Paper mill rollers manufacturers