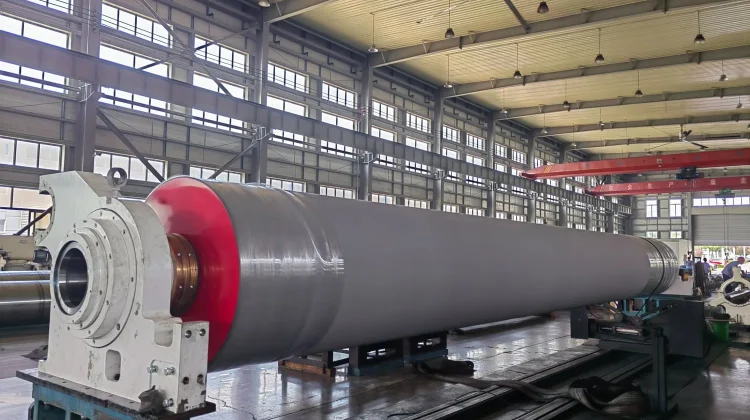
Finding the Right Pulp and Paper Machinery Suppliers
In the intricate world of pulp and paper production, the backbone of efficient operation isn’t just raw materials or skilled labor; it’s the sophisticated machinery that transforms wood pulp or recycled fibers into the paper products we use daily. From initial fiber preparation to the final winding and packaging, every step relies on precision-engineered equipment. Choosing the right pulp and paper machinery suppliers is not merely a procurement decision; it’s a strategic partnership that impacts productivity, product quality, operational costs, and long-term sustainability. The machinery must be robust, reliable, and capable of meeting demanding production schedules. Frankly speaking, downtime due to equipment failure can be incredibly costly, disrupting supply chains and eroding profitability. Therefore, selecting suppliers with a proven track record, deep technical expertise, and a commitment to service is paramount. This introductory exploration sets the stage for understanding the critical role these suppliers play and the factors that should guide your selection process, ensuring your mill operates at its peak potential. It’s worth noting that the quality and performance of your machinery directly influence the competitiveness of your final product in the market.
Understanding the Range of Pulp and Paper Machinery
The scope of equipment needed in a pulp and paper mill is vast and varied, covering distinct stages of the manufacturing process. First, there’s the pulping phase, which involves breaking down raw materials into a fibrous pulp. This requires chippers, digesters, refiners, screens, and washing equipment. The quality of the pulp significantly influences the final paper properties, so machinery in this stage must be highly efficient and capable of precise fiber treatment. Following pulping is the papermaking process itself, arguably the most iconic part. This involves complex machines like headboxes (distributing the pulp slurry), wire sections (water removal), press sections (further dewatering), and dryer sections (final moisture removal). These machines are often massive, requiring intricate design and manufacturing expertise. Then come the finishing processes: calendering (smoothing and thickness control), coating (applying special surfaces), slitting (cutting into rolls), and winding. Each machine in this sequence needs to integrate seamlessly with the others. Interestingly enough, advancements in these machines are constantly pushing the boundaries of speed, efficiency, and paper quality. Therefore, finding pulp and paper machinery suppliers who can offer expertise across this entire spectrum, or specialize deeply in a critical area, is crucial for ensuring operational harmony and achieving desired product specifications.
Essential Equipment Categories and Their Role
Diving deeper into the machinery, let’s consider the critical categories. In the pulping area, primary equipment includes debarkers and chippers for wood preparation, followed by digesters for chemical pulping or mechanical pulping equipment like refiners. Screening and cleaning systems are essential for removing impurities. Water treatment and fiber recovery systems are also vital components, emphasizing sustainability and efficiency. For papermaking, the heart is often the paper machine itself, a complex assembly spanning hundreds of feet. Key sections like the forming section (Fourdrinier or gap former), press section, and dryer section each play a specific, indispensable role in forming the paper sheet. Finishing equipment includes calenders for surface properties, winders for creating usable rolls, and often coaters for producing specialized papers. Selecting suppliers who excel in the engineering and manufacturing of these core components is non-negotiable for reliable production. Consider, for instance, the precision required in a headbox to ensure uniform fiber distribution – a fundamental step for paper quality. The reliability of a dryer section, with its many steam-heated cylinders, is critical for throughput and energy efficiency. These are not just machines; they are complex systems that demand high-level engineering and manufacturing quality.
Choosing the Right Pulp and Paper Machinery Suppliers: Key Criteria
So, how do you navigate the landscape of potential pulp and paper machinery suppliers? It boils down to a few key criteria that extend far beyond just the initial purchase price. Firstly, technology and innovation are paramount. The industry is constantly evolving, with new materials, processes, and automation technologies emerging. A leading supplier should be at the forefront of these developments, offering machinery that is not only reliable but also incorporates the latest advancements for improved efficiency, reduced energy consumption, and enhanced product quality. Look for suppliers who invest heavily in R&D and can demonstrate a clear understanding of future industry trends. Secondly, quality and reliability are non-negotiable. Machinery in a paper mill operates continuously under demanding conditions. The equipment must be built to last, with high-quality materials and robust engineering. Ask about the supplier’s manufacturing standards, quality control processes, and the lifespan of their equipment. A supplier confident in their product’s durability will likely offer strong warranties. Have you ever wondered about the true cost of poor-quality machinery? It’s not just the repair bill; it’s the lost production, wasted raw materials, and damaged reputation. That’s why investing in quality from reputable pulp and paper machinery suppliers is a long-term cost-saving measure.
Evaluating Supplier Capabilities and Expertise
Beyond the machinery itself, the supplier’s capabilities are equally critical. This includes their engineering expertise, project management skills, and ability to provide customized solutions. A supplier should ideally have experienced engineers who understand the nuances of pulp and paper manufacturing and can work with you to design or modify equipment to meet your specific needs and mill layout. Many mills have unique requirements based on the type of fiber used, the grade of paper produced, or space constraints. The ability to provide custom paper machine manufacturing or tailored modifications to standard equipment is a significant advantage. Furthermore, consider their experience with projects similar to yours – whether it’s a complete new line installation, a major upgrade, or troubleshooting complex issues. A supplier with relevant experience will anticipate challenges and deliver solutions more effectively. In my experience, a supplier’s technical team should feel like an extension of your own, collaborative and knowledgeable. Their understanding of industrial pulp processing equipment and its interaction with the entire mill process is invaluable. Don’t hesitate to ask for case studies or references from other customers to gauge their capabilities and project success rate.
The Importance of After-Sales Service and Support
Purchasing pulp and paper machinery is a significant investment, and the relationship with the supplier doesn’t end when the equipment is installed. After-sales service and support are absolutely vital for ensuring the long-term performance and longevity of the machinery. This includes installation assistance, operator training, maintenance support, and readily available spare parts. A good supplier will offer comprehensive training programs to ensure your staff can operate and maintain the equipment safely and efficiently. Proactive maintenance services, including regular inspections and preventive maintenance programs, can help identify potential issues before they lead to costly breakdowns. Furthermore, access to spare parts is critical; delays in getting a replacement part can bring an entire production line to a halt. A supplier with a well-organized spare parts inventory and efficient logistics can save you significant downtime and money. Consider their technical support capabilities – do they offer remote diagnostics? Is a rapid response team available for urgent issues? The quality of paper mill equipment maintenance and support provided by the supplier can make a huge difference in your mill’s overall uptime and operational efficiency. It’s about partnering with suppliers who are committed to your success long after the initial sale.
Technological Advancements Shaping Pulp and Paper Machinery
The world of pulp and paper machinery is constantly evolving, driven by technological advancements aimed at improving efficiency, reducing environmental impact, and enhancing product quality. Automation and digitalization are major trends, with advanced control systems, sensors, and data analytics enabling more precise control over the manufacturing process, optimizing resource usage, and predicting maintenance needs. Energy efficiency is another critical focus area. Modern machines are designed to consume less energy, whether through optimized drying processes, more efficient motors, or heat recovery systems. Given the high energy consumption of paper mills, even small improvements in efficiency can lead to significant cost savings and a reduced carbon footprint. Sustainability is also influencing machinery design, with innovations supporting the use of recycled fibers, reducing water consumption, and minimizing waste. Some suppliers are developing equipment specifically designed for processing alternative fibers or improving deinking processes. Choosing pulp and paper machinery suppliers who are investing in these areas ensures your mill remains competitive and environmentally responsible. It’s fascinating to see how technology, like advanced sensors and AI, is transforming even traditional processes within the mill, offering unprecedented levels of insight and control.
The Value of Customization and Flexibility
While standardized machinery forms the core of many operations, the ability to customize or adapt equipment is often a significant advantage. Each paper mill is unique, with its own layout, existing infrastructure, specific raw materials, and desired product grades. Off-the-shelf solutions may not always provide the optimal performance or seamless integration required. This is where the value of suppliers offering custom paper machine manufacturing or flexible design options comes into play. Whether it’s modifying machine dimensions to fit an existing building, designing specialized headboxes for unique fiber blends, or incorporating specific control system requirements, customization can significantly improve efficiency and product quality. A supplier willing and able to work closely with your engineering team to understand your specific needs and develop tailored solutions demonstrates a higher level of partnership. This capability is particularly important for mills producing specialty papers or facing unique operational challenges. Don’t underestimate the impact that equipment designed specifically for your operation can have on throughput and finished product characteristics. Why settle for a general solution when a customized approach can unlock greater potential?
Partnering for Long-Term Success
Ultimately, the relationship with your pulp and paper machinery suppliers should be viewed as a long-term partnership. It’s not just about the transaction; it’s about collaborating with companies that understand your business goals and are committed to supporting your success over the entire lifecycle of the equipment. This includes not only reliable machinery and excellent service but also ongoing technical support, upgrades, and advice on optimizing your processes. A strong partnership is built on trust, communication, and mutual understanding. Look for suppliers who are transparent in their dealings, responsive to your needs, and proactive in offering solutions or improvements. Many experts agree that establishing close ties with key suppliers leads to smoother operations, faster problem resolution, and access to valuable industry knowledge. These suppliers are often at the forefront of new developments and can provide insights that help you stay ahead of the competition. Think of them not just as vendors, but as strategic allies in your production journey. They are key players in ensuring your paper mill equipment maintenance is effective and your machinery continues to perform optimally year after year.
Our Role in Supporting Your Operations
Understanding the critical requirements and challenges faced by pulp and paper manufacturers, our focus is on providing machinery and solutions that address these specific needs. We aim to be among the leading pulp and paper machinery suppliers by offering a range of equipment designed for reliability, efficiency, and performance across various mill operations. We recognize the importance of technology and invest in R&D to provide modern solutions that help mills improve productivity, reduce costs, and enhance product quality. Our expertise spans key areas of pulp processing and papermaking, allowing us to offer equipment that integrates effectively within existing mill infrastructures or serves as the foundation for new lines. We understand that each mill has unique requirements, and we are committed to working closely with our clients to provide tailored solutions, whether through standard machinery or specific customizations. Our commitment extends beyond the sale, with a focus on providing dependable after-sales support and technical assistance to ensure your operations run smoothly. We believe in building lasting partnerships based on mutual trust and a shared goal of operational excellence.
Next Steps in Your Supplier Search
Embarking on the journey to find the ideal pulp and paper machinery suppliers requires careful consideration and thorough evaluation. Start by clearly defining your specific machinery needs, including required capacity, desired product quality, budget constraints, and integration requirements with existing equipment. Research potential suppliers, looking at their history, reputation, product range, and customer base. Don’t be afraid to request detailed technical specifications, performance data, and energy consumption figures for their equipment. Visiting supplier manufacturing facilities and speaking with their engineers can provide valuable insights into their capabilities and quality control processes. Request references from other customers and take the time to speak with them about their experiences regarding equipment performance, reliability, and after-sales support. Compare not just the initial price, but the total cost of ownership, including energy consumption, maintenance requirements, spare parts availability, and expected lifespan. Making an informed decision is crucial for the long-term success and profitability of your mill. This process, while demanding, is essential for securing the right partners who will contribute significantly to your operational efficiency and competitive edge.
For more detailed information, please visit our official website: Pulp and paper machinery suppliers